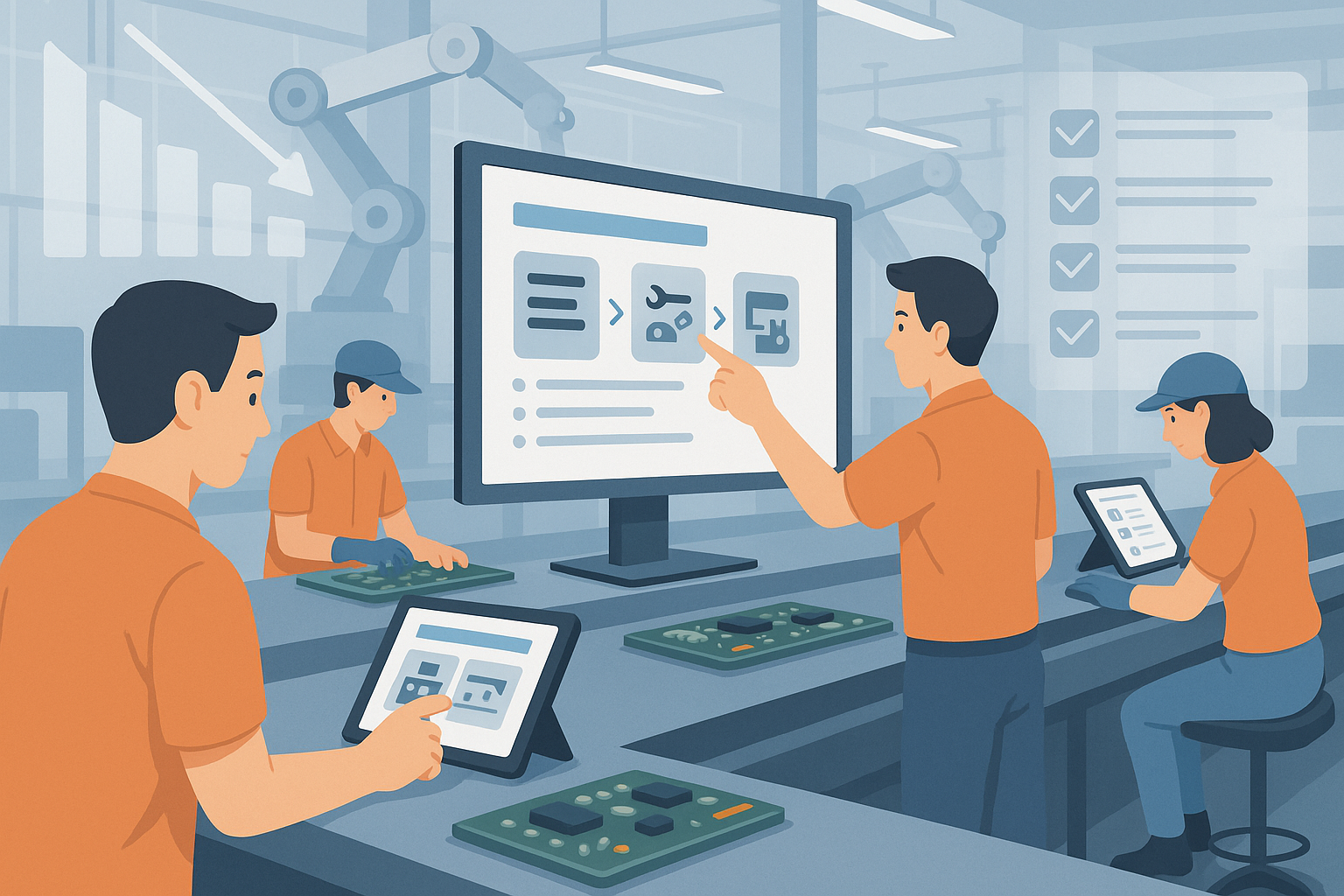
電子機器は多品種少量生産が当たり前となり、組立工程は日々入れ替わる部材・仕様への即応が求められます。こうした環境では、担当者ごとに「やり方」が異なる属人化が進み、不良率や再作業コストが膨張しがちです。
本記事では、マニュアルをモジュール化しクラウド(e-manual)上で一元管理した結果、組立ラインの不良率を半減させたC社の実践例を詳しく紹介します。
「実際にどう進めればいいのか?」をイメージできるように、現場で再現可能なステップと、現場担当者が直面しがちな注意点を具体的に解説します。
課題:電子機器組立マニュアルに潜むリスク
現場ヒアリングで顕在化した主な課題は次のとおりです。
- 作業者や部署ごとにフォーマットが違い、改訂履歴を追えない
- 仕様差分が多く、最新版がどれか現場で判断できない
- 専門用語が統一されておらず、誤解が原因のヒューマンエラーを誘発
- 教育資料が散在し、新人育成に平均120時間を要していた
これらは「情報の一元管理不足」と「標準ルール欠如」が根源であり、ライン停止や顧客クレームの直接原因になっていました。
解決策:マニュアル標準化×e-manual導入
C社は上流(設計)と下流(製造・サービス)の混在ドキュメントを棚卸しし、共通・固有コンテンツを分離してモジュール化。そのうえで、クラウド型e-manualに移行しました。結果として、
- モジュール管理で、一度の修正が関連マニュアルへ即時反映。
- 用語フィルターが、バラつきを自動検出しワンクリック統一。
- 承認ワークフローにより、未検証情報の現場流出を防止。
- HTML/PDF同時生成で、紙・Web双方への配布を省力化。
- 動画リンクを挿入し、作業イメージを直感的に共有。
これらの機能が「最新版を正確に配布し続ける仕組み」を作り上げ、工程品質に直結しました。
実装プロジェクトの進め方と成功のポイント
まず文書体系マップを作成し、既存資料の関係性と重複を可視化しました。次に、標準目次を決定し要素単位(トピック)で共通化。ここまでに3か月を要しましたが、以降の改訂工数は70%削減されています。
成功を左右したポイントは次の5つです。
- 経営層スポンサーの確保 ― 品質指標(不良率)をKPIに設定
- 専門チームを編成し、設計・品質・現場を横串で統括
- ガイドラインに用語辞書と画像スタイルを盛り込み、迷いを排除
- デジタル教育(動画・AR)を並行導入して習熟度を定量把握
- 改訂後24時間以内に現場へ通知する自動アラートを設定
成果:数字で見る改善効果
C社では導入から1年で次の成果が確認されました。
- 不良率:2.1% → 1.0%(▲52%)
- 教育工数:新人1名あたり120h → 60h
- 印刷費:年 900万円削減(オンデマンド印刷活用)
- 設計者の執筆時間:月30h相当を本来業務へ再配分
さらに、ワンソースを活かして英語・中国語版を短期間で公開し、海外拠点でも同品質の作業標準を展開できています。
まとめ:実践アクションステップ
- 既存マニュアルを棚卸しし、共通/固有を分類する
- 標準目次と用語辞書を策定してガイドラインを明文化
- モジュール化とクラウドツールで改訂フローを自動化
- 動画・VRなど視覚メディアを取り込み教育を高速化
- KPI(不良率・教育時間・改訂工数)を継続モニタリングし効果を可視化
これらを段階的に実行すれば、不良率低減と生産性向上を同時に実現できます。将来的にはスマートグラス連携や設計BOM連動に発展させ、完全な「生成AI+ARマニュアル」へ進化させることも可能です。
FAQ
Q1. 導入コストは高くないですか?
初期整備に工数はかかりますが、印刷費と不良削減効果で1~2年で投資回収した事例が多いです。
Q2. 多品種ラインでも維持できますか?
モジュール化により共通部を流用できるため、品種が増えるほど効果が高まります。
Q3. 動画やAR用コンテンツは必須ですか?
必須ではありませんが、教育効率と理解度向上に寄与するため並行検討を推奨します。
Q4. 海外拠点への展開方法は?
XMLエクスポートで翻訳メモリに連携し、多言語版を短期間で生成可能です。
この記事を書いた人
編集部