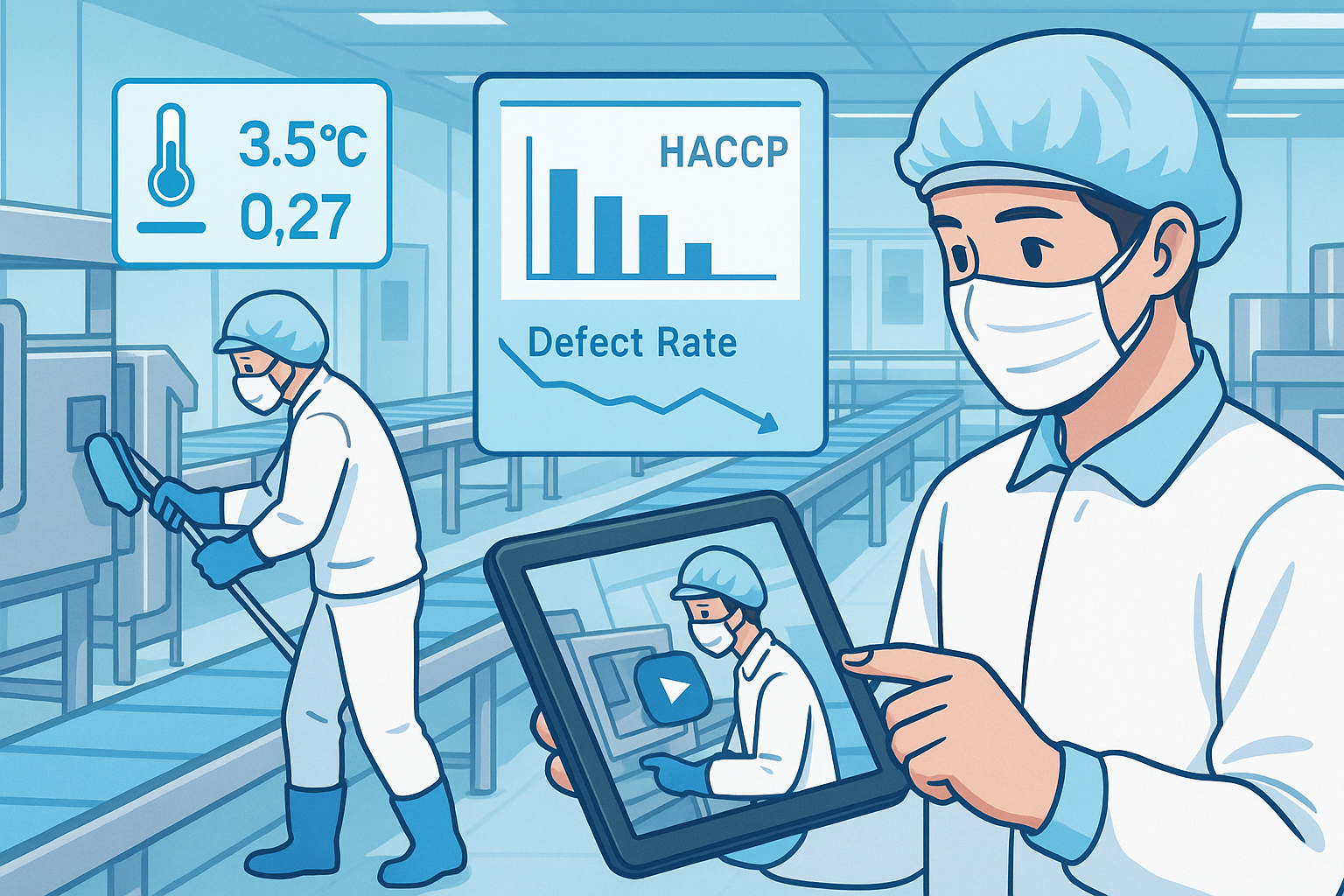
HACCP義務化で衛生基準が高まる一方、多品種少量生産で現場は複雑化しています。本記事では作業標準化・工程管理・教育効率化をキーワードに、冷凍食品メーカーA社のマニュアル刷新事例をご紹介します。
衛生管理と効率化を両立させる難題
食品製造の現場では、HACCP対応による厳格な衛生管理が日常業務に組み込まれました。しかし、消費者ニーズの多様化にともなう製品ラインアップの拡大は、工程の入れ替え頻度を増加させ、手順書の肥大化と最新版管理の煩雑化を招いています。結果として、ベテラン頼みの属人的作業から抜け出せず、新人教育コストが増大し、不良発生率や検査不合格件数も高止まりする傾向が見られます。こうした現場を「見える化」し、作業標準化を推進するマニュアル改革は、今や競争力を左右する戦略課題です。
食品製造業特有の課題
ある冷凍食品工場では、PDF手順書は300ページを超えていました。操作方法を探すのに平均90秒を要し、1日に平均8回のライン切替が発生しますが、その間ラインは停止したままです。加えて、金属検出器の点検漏れが5%発生し、年に10件の拭き取り検査不合格ロットが出るなど、衛生リスクが顕在化していました。これらは「複雑工程」「高品質要求」「少量多品種」という食品製造業ならではの要件が絡み合って生じる典型的な課題です。
改革プロジェクトの進め方と体制
A 社は品質管理部・製造部・情報システム部から 12 名を選抜し、現場リーダーを共同オーナーに据えた横断チームを編成しました。チームは隔週で現場ヒアリングとプロトタイプ評価を繰り返し、ガントチャートで進捗と課題を共有。現場の疑問をその場で解消する「カンバンミーティング」を導入し、現場の合意形成を迅速に行ったことがスムーズな導入を後押ししました。
採用したマニュアル形式と運用方法
まずはマニュアルを見直した結果、1ページ1工程の形式を採用し、工程ごとに統一された構造になるように刷新しました。さらに工程間のリンクを設定することで、すぐに次の工程に飛べるようになりました。
あわせて、60~90秒の作業動画も作成し、現場タブレットでQRコードを読み込むことですぐに再生できるようにしました。さらに、温度・金属検出ログを自動で集計する衛生管理ダッシュボードを連携し、異常値発生時は手順書の該当ページへワンクリックで遷移できる仕組みを構築しました。
得られた効果
導入から6か月後、手順検索時間は平均15秒に短縮され、ライン停止時間が大幅に削減されました。新人の作業不良率は12%から3%に低下し、拭き取り検査の不合格は年1件に抑制。ライン稼働率は4.5% 向上し、初年度のROIは135%に達しました。現場リーダーは「手順書と動画の組み合わせで教育時間が3分の1になり、ベテランのノウハウが共有財産になった」と語ります。
成功のポイント
- 現場巻き込み型PDCAを短サイクルで回し、実際に使える形式を検討した
- 同一構図・同一音声ルールで動画の品質を均一化し、再撮影を簡易化
- 5S活動と連動させ、「使えるマニュアル」を合言葉に現場の抵抗感を低減
- KPIを作業者目線(手順検索時間・動画再生回数など)で設定し効果を可視化
まとめ:実践のためのアクションステップ
まず、既存手順書を分析して検索時間と不良率を測定し、不良リスクの高い工程から優先的に着手してください。次に、モジュール化されたプロトタイプを作り、現場で即使用してもらうサイクルを2週間ごとに回します。最後に、ダッシュボードでKPIをモニタリングし、成功したフォーマットを水平展開することで、作業標準化と品質改善を同時に実現できます。
FAQ
Q1. デジタルマニュアルの初期費用はどの程度ですか?
中小規模工場であれば、タブレット数台とクラウドサービスを含めて100万〜300万円が一般的です。
Q2. HACCP文書との統合は容易でしょうか?
手順をHACCPの文書体系に合わせて整理すれば、マニュアル刷新と衛生管理の整合性を高めつつ工数を削減できます。
Q3. 動画更新の負荷が心配です。
工程変更時のみ撮り直す短尺動画に絞り、撮影テンプレートを用意することで運用負荷を最小化できます。
Q4. 紙マニュアルを完全に廃止すべきですか?
停電時や端末故障時のバックアップとして、主要工程だけ紙を残す二重化運用を推奨します。
Q5. 他工場へ展開する際の注意点は?
設備番号や作業者動線といったレイアウト変数をパラメータ化し、現場固有情報を切り離すと再利用性が高まります。
この記事を書いた人
編集部