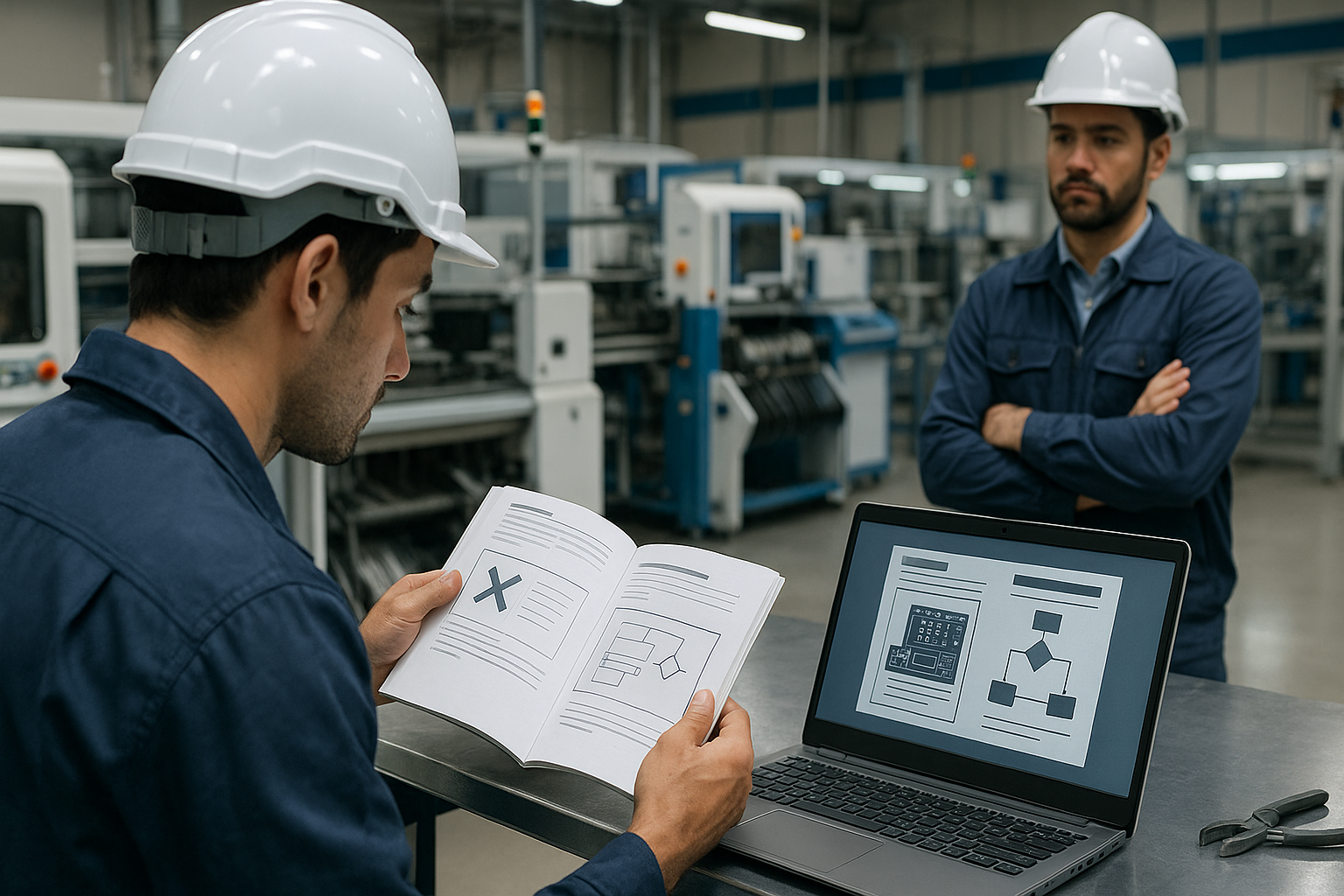
製造現場におけるマニュアルは、「あるだけ」で終わってしまっては意味がありません。現場で本当に活用されるマニュアルとは、どのような条件を満たしているのでしょうか。この記事では、マニュアルが現場で定着し、活用されるための工夫や改善ポイントを掘り下げ、成功事例と失敗事例の両方から、読者がすぐに活かせる実践的な知見をお届けします。
※本記事は、当社業務の実態をもとに構成した【仮想インタビューコンテンツ】です。登場人物・部署名などはすべて仮想のものです。
インタビュー対象者プロフィール
氏名(仮名):佐藤 拓也
所属: 生産技術部・現場リーダー
経験年数:現場歴18年(うちリーダー職12年)
管理ライン:自動実装ライン・検査ライン(計20名程度の作業員を指導)
現場での課題とマニュアルの位置づけ
Q:現在の製造ラインでは、どのような課題があると感じていますか?
佐藤:
一番大きな課題は「作業の属人化」です。特定のベテラン作業員にしかできない業務が多く、新人や他ラインの応援者が入ったときに教育コストが非常に高くなります。マニュアルを整備する目的も、作業の標準化と再現性の確保が第一です。
🔍ポイント解説
属人化とは、特定の人物に作業やノウハウが依存する状態を指します。製造業では品質のばらつきや教育の非効率化の原因になります。
活用されるマニュアルの条件とは
Q:現場で「実際に使われている」と感じるマニュアルの特徴を教えてください。
佐藤:
現場で本当に使われるマニュアルには、以下の条件が揃っています:
- 作業時間内に確認できる構成になっていること→ 文量が多すぎると、読んでもらえません。1作業=1ページ、1工程=1チャートに収めるなど、時間内で読める工夫が必要です。
- 写真や図が中心で、直感的に理解できること→ 特に作業の「やってはいけないポイント」は赤枠や吹き出しで強調すると、一目で理解しやすくなります。
- 現場のレイアウトや設備に合っていること→ 汎用マニュアルではなく、実際の機種や型番、使用工具に合わせた内容であることが重要です。
成功事例と失敗事例から学ぶ
Q:過去にマニュアル作成でうまくいった例と、逆に失敗した例を教えてください。
佐藤:
成功例としては、ライン変更時に新マニュアルを「動画+紙」で整備したことがあります。動画では「手の動かし方」や「作業スピード感」が伝えやすく、新人が独学でも理解できるようになりました。
一方で失敗例は、全社で統一された「ISO対応マニュアル」をそのまま現場に落とし込んだケースです。文書は立派でしたが、読む人がいない。実際に誰も開いておらず、現場には掲示板に手書きの注意メモが貼られていました。
🚫失敗の教訓
フォーマットや基準が重要なのは当然ですが、実際に使う人の視点を無視すると「誰のためのマニュアルか分からない」状態になってしまいます。
作業員の声と現場のリアル
Q:作業員からのマニュアルに対する反応や意見にはどんなものがありますか?
佐藤:
現場の作業者からは、こんな声が多く聞かれます。
- 「どこを見ればいいのかすぐ分かるようにしてほしい」
- 「文字が多いと読む気にならない」
- 「不具合があったときの対処方法も書いてあると助かる」
ですので、最近は作業工程だけでなく、「エラー発生時の対処チャート」も一緒に付けるようにしています。特に夜勤帯など、すぐに上長に聞けない場面では重宝されます。
✏️「エラー発生時の対応チャート」の例
まとめと実践アドバイス
Q:最後に、マニュアル作成担当者へのアドバイスをお願いします。
佐藤:
「書いた人が使ってほしいこと」と「現場が本当に使いたいこと」にはギャップがあります。まずはそのギャップを埋めることが第一歩です。以下のアクションをおすすめします:
- 作成前に現場作業者のヒアリングを行うこと
- 「読む側の時間・視点・状況」に立って構成を考えること
- 紙・電子・動画など複数フォーマットでの提供を検討すること
- 初版完成後も定期的にフィードバックを受けて更新すること
現場にとっての「よいマニュアル」とは、作業を止めずに迷わず進められるマニュアルです。それを目指して、現場との距離を縮めていってほしいと思います。
この記事を書いた人
編集部