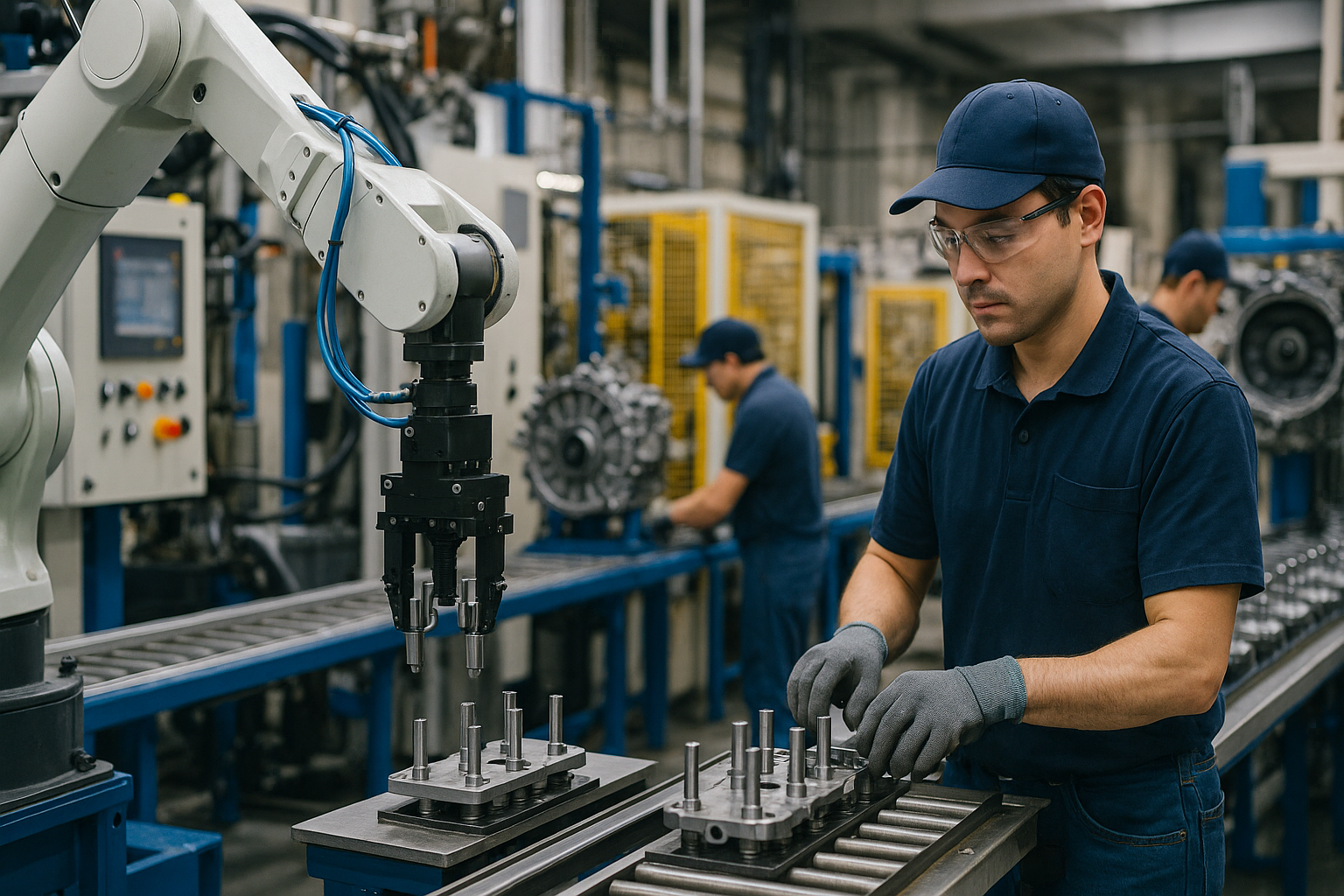
自動車部品製造業では、複雑かつ多工程のライン、多品種少量生産、そしてミクロン単位の品質要求が日常です。その現場で「属人化した手順書がボトルネックとなり、生産性が伸び悩む」という課題を抱える企業は少なくありません。本記事では、ある中堅サプライヤーA社がマニュアル改革によって総合設備効率(OEE)を15% 向上させた事例を基に、成功のポイントを解説します。
課題の背景
高度化する品質要求と多品種少量
電動化・軽量化の流れにより部品バリエーションが急増し、工程切替頻度は月平均 12 回 ➜ 20 回 に増加。1/1000 mmレベルの公差管理が求められる中、準備ロスと人的ミスが顕在化していました。
改革前の問題点
- 手順書が設備ごとに散在し、検索に平均 7 分
- 改版履歴が残らず、不適格手順での作業が原因の品質不良が 月間3件
- 新人教育に 60 時間、習熟度に大きなばらつき
改革プロジェクトの全体像
A社は「工程横断チーム(工程・品質・教育)」と「IT推進室」の二層体制を構築し、半年間で次のフェーズを実行しました。
フェーズ | 期間 | 主要活動 |
---|---|---|
現状分析 | 1か月 | マニュアル棚卸し、参照頻度調査 |
設計 | 2か月 | 新フォーマット策定、タグ設計 |
実装 | 2か月 | 既存手順書移行、動画撮影 |
定着 | 1か月 | 5S+OJT運用、効果測定 |
具体的アプローチ
3-1. マニュアル体系の再設計
- 3層構造(ライン共通・設備固有・品番固有)で冗長排除
- ページ冒頭に「工程コード」「変更履歴」をメタデータとして埋め込み、全文検索と改版管理を両立
3-2. フォーマット統一と可視化
- 文書+動画をセット化し、現場の作業台にQRコードを掲示
- 写真注記は赤枠と矢印のみで視覚ノイズを排除
- Gitベースのバージョン管理で過去版を自動保存
指標 改革前 改革後 改善率 OEE 68% 78% +15% 品質不良率 0.40% 0.25% -38% 教育時間 60 h 42 h -30%
3-3. 現場主導の改善サイクル
- 日次「30分カイゼン枠」を設定し、作業者が自分で手順書を更新
- 週次レビューで品質・安全・生産性への影響を評価
- 改版承認は ワークフロー+電子署名 でリードタイムを1/3に短縮
成果と効果測定
- OEE:68% ➜ 78%(+15%)
- 品質不良率:0.40% ➜ 0.25%
- 教育時間:60 h ➜ 42 h(–30%)
- 作業者アンケート満足度:3.1 ➜ 4.2/5
導入時の障壁と克服策
障壁 | 原因 | 克服アプローチ |
---|---|---|
現場の抵抗感 | 「書類作成=残業」の固定観念 | カイゼン枠を勤務時間内に設定し、成果を即フィードバック |
ITリテラシー差 | PC操作に不慣れ | タブレット+写真中心テンプレートで入力負荷を軽減 |
データ整合性 | 旧版と新版の混在 | 一括移行後、旧版は閲覧専用とし誤使用を防止 |
他業種への応用可能性
食品・医薬品のようにGMPやHACCPが求められる業界でも「層別マニュアル+動画連携」は有効です。特に段取替えが頻繁なラインでは、品番固有動画が段取時間を10%以上短縮する事例が確認されています。
まとめとアクションステップ
本記事では、体系再設計・フォーマット統一・現場主導の改善サイクルという3つの鍵を紹介しました。まずは次の3ステップから着手しましょう。
- 現状棚卸し
- すべての手順書を洗い出し、参照頻度と改版履歴を可視化
- 共通フォーマット策定
- 工程コード・変更履歴を必須項目に設定し、検索軸を標準化
- 現場改善枠の設定
- 小さく始め、改善を習慣化する仕組みを作る
15%の生産性向上は決して夢物語ではありません。自社の現場に合わせて、本日から一歩を踏み出してみてください。
この記事を書いた人
編集部