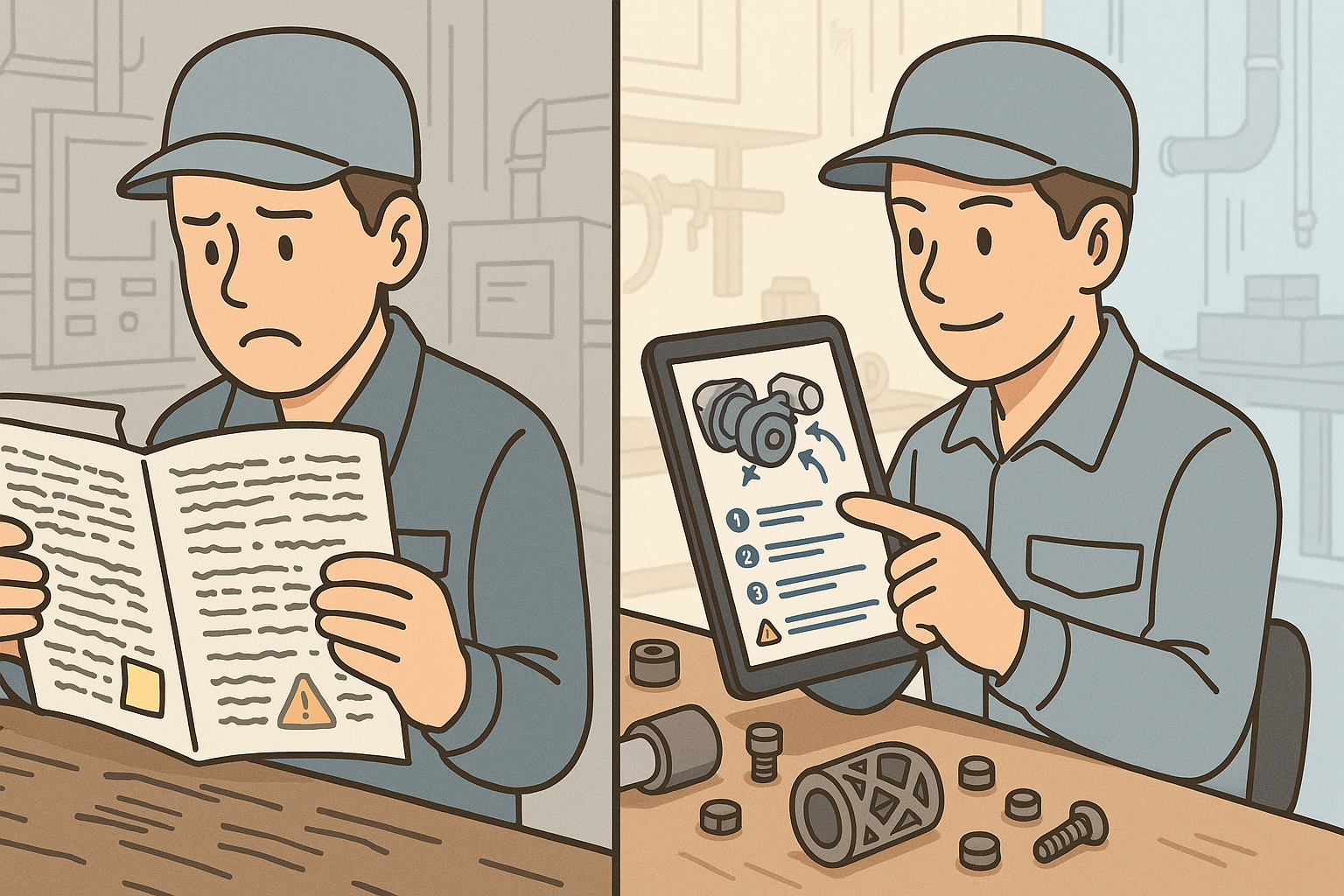
製造業の現場で「マニュアルはあるのに活用されていない」「マニュアルを見ても作業がうまくできない」という課題を抱えていませんか?実は、マニュアルの質が現場の生産性や品質に大きな影響を与えています。本記事では、「使われないマニュアル」と「現場で活用される効果的なマニュアル」の違いを、具体的なビフォーアフター比較を通じて解説します。改善のポイントとともに、実際の製造業での成功事例も紹介しますので、自社のマニュアル改善にぜひお役立てください。
目次
マニュアルの質が製造現場に与える影響
良質なマニュアルと不十分なマニュアルでは、現場にどのような違いが生まれるのでしょうか。
1-1. 悪いマニュアルがもたらす問題
- 品質のばらつき:作業者による解釈の違いが発生
- 作業ミスの増加:重要ポイントが伝わらない
- 技能伝承の困難:暗黙知が伝わらない
- マニュアル不信:「見ても役に立たない」と使われなくなる
1-2. 良いマニュアルがもたらす効果
- 品質の安定化:誰が作業しても同じ結果に
- 習熟時間の短縮:初心者が早く一人前に
- 改善の基盤:標準化があってこその改善
- 安全性の向上:リスクポイントの確実な伝達
電子部品メーカーA社では、組立マニュアルを全面的に改訂したところ、新人の習熟期間が従来の半分に短縮され、不良率も5%から1%以下に低減しました。
作業手順の記載方法:曖昧な指示から明確な指示へ
2-1. ビフォー(悪い例)
部品Aを取り付け、適切に調整してからネジで固定する。
問題点:
- 「適切に」という曖昧な表現
- 複数の作業を一文にまとめている
- 具体的な数値や基準がない
- 作業の順序が不明確
2-2. アフター(良い例)
1. 部品Aを取り出す。
2. 取付け面の汚れを拭き取る。
3. 部品Aの凸部を本体の凹部に合わせる。
4. 部品Aを押し込み、カチッと音がするまではめ込む。
5. トルクレンチでネジを12N・mで締め付ける。
改善ポイント:
- 一文一動作で明確に記載
- 具体的な数値や判断基準の明示
- 省略されがちな前準備も記載
- 番号付けで手順を明確化
自動車部品メーカーB社では、「一文一動作」「具体的数値の明示」を徹底したマニュアル改訂により、作業者間のばらつきが大幅に減少し、初期不良率が60%低減しました。
視覚情報の活用:文字偏重から視覚重視へ
3-1. ビフォー(悪い例)
文字だけの長い説明で、重要ポイントが埋もれている。
部品Cを取り付ける際は、まず部品の向きを確認し、矢印マークが上を向くようにする。 次に左側のツメを先に差し込み、その後右側を押し込む。 この時、無理な力を加えないように注意する。 正しく取り付けられると、両端のツメがカチッとはまる音がする。
3-2. アフター(良い例)
ポイントを視覚化し、簡潔な説明文を添える。
改善ポイント:
- 文字情報と視覚情報のバランス
- 重要ポイントの視覚的強調
- ステップごとの写真や図解
- 簡潔な説明文の併記
電子機器メーカーC社では、従来の文字中心マニュアルから視覚情報重視のマニュアルに変更したところ、多国籍作業者のいる工場での理解度が向上し、組立時間が25%短縮されました。
安全・品質情報の記載:形式的な記載から効果的な記載へ
4-1. ビフォー(悪い例)
マニュアルの冒頭に一般的な注意事項をまとめて記載。
【安全上の注意】
1. 作業時は保護手袋を着用すること
2. 部品の取り扱いに注意すること
3. 異常を感じたら作業を中止すること
...(長いリストが続く)
問題点:
- 具体的な危険箇所や理由が不明
- 作業手順とは分離されている
- 一般的すぎて印象に残らない
- 長すぎて読まれない可能性が高い
4-2. アフター(良い例)
具体的な作業ステップの直前に関連する注意点を記載。
STEP 5: ケーブルの接続
⚠️警告:感電の危険!
必ず電源がOFFになっていることを確認してから作業を行う。
(理由:最大240Vの電圧があり、感電する恐れがあります)
1. コネクタの向きを確認する(赤いマークを上に)
2. まっすぐ差し込む(斜めに差すと端子が曲がる)
...
改善ポイント:
- 関連する作業の直前に警告を配置
- 具体的な危険内容と理由の明示
- 視覚的な警告マークの活用
- 重要度に応じた表現の使い分け
化学メーカーD社では、作業手順書の安全情報に「なぜその対策が必要か」の理由を明記する形式に変更したところ、作業者の安全意識が向上し、軽微な事故も含めた災害発生率が前年比40%減少しました。
マニュアルの構成と整理:探しにくさから使いやすさへ
5-1. ビフォー(悪い例)
情報が整理されておらず、必要な情報を探すのに時間がかかる。
- 目次や見出しがない
- 長い文章が続き、段落分けが不適切
- 重要度による情報の優先順位付けがない
- 関連情報が分散している
5-2. アフター(良い例)
情報を整理し、必要な情報にすぐにアクセスできる。
改善ポイント:
- 明確な目次と見出し
- 情報の階層構造化
- 視覚的なインデックス(タブ、色分けなど)
- 関連情報のグルーピング
- デジタル版でのハイパーリンク活用
食品メーカーE社では、作業マニュアルを「基本作業」「品質チェック」「トラブル対応」などのセクションに色分けして整理し、インデックスタブを付けたところ、マニュアル参照時間が従来の3分の1に短縮されました。現場からは「必要な情報がすぐに見つかるようになった」との評価を得ています。
作業の根拠と背景:手順だけから理解促進へ
6-1. ビフォー(悪い例)
手順のみを記載し、「なぜそうするのか」の説明がない。
モーター取付けボルトは、必ず対角順に均等に締め付けること。
問題点:
- 理由の記載がなく、重要性が伝わらない
- 応用や判断が必要な場面での対応が難しい
- 作業者の理解や記憶に残りにくい
6-2. アフター(良い例)
作業の理由や背景を簡潔に説明。
モーター取付けボルトは、必ず対角順に均等に締め付ける。
【理由】偏った締め付けを行うと、モーターが傾き、振動や軸ズレの原因となる。
これにより、騒音増加や部品の早期摩耗につながる。
改善ポイント:
- 「なぜそうするのか」の理由説明
- 守らなかった場合の影響を明示
- 理解を促す簡潔な補足情報
- 重要なポイントの科学的・技術的背景
機械メーカーF社では、マニュアルに「理由」を追加する改訂を行ったところ、作業者の理解度が向上し、「言われたとおりにやる」から「考えながら作業する」文化への変化が生まれました。これにより、作業者からの改善提案数が増加し、品質向上につながっています。
まとめ:マニュアル改善のためのアクションステップ
効果的なマニュアルへ改善するためのアクションステップをまとめます。
- 現状マニュアルの問題点を特定する(現場の声を収集)
- 一文一動作の原則で曖昧な表現を排除する
- 視覚情報を効果的に活用する
- 安全・品質情報を関連する作業の直前に配置する
- 情報を整理し、必要な情報にすぐアクセスできるようにする
- 作業の理由や背景を簡潔に説明する
- 実際の現場で検証し、継続的に改善する
マニュアルは作って終わりではなく、継続的に進化させるべき「生きた文書」です。現場の声を反映しながら改善を重ね、真に現場で活用されるマニュアル作りを目指しましょう。本記事で紹介したビフォーアフターの比較を参考に、ぜひ自社のマニュアル改善に取り組んでみてください。
この記事を書いた人
編集部