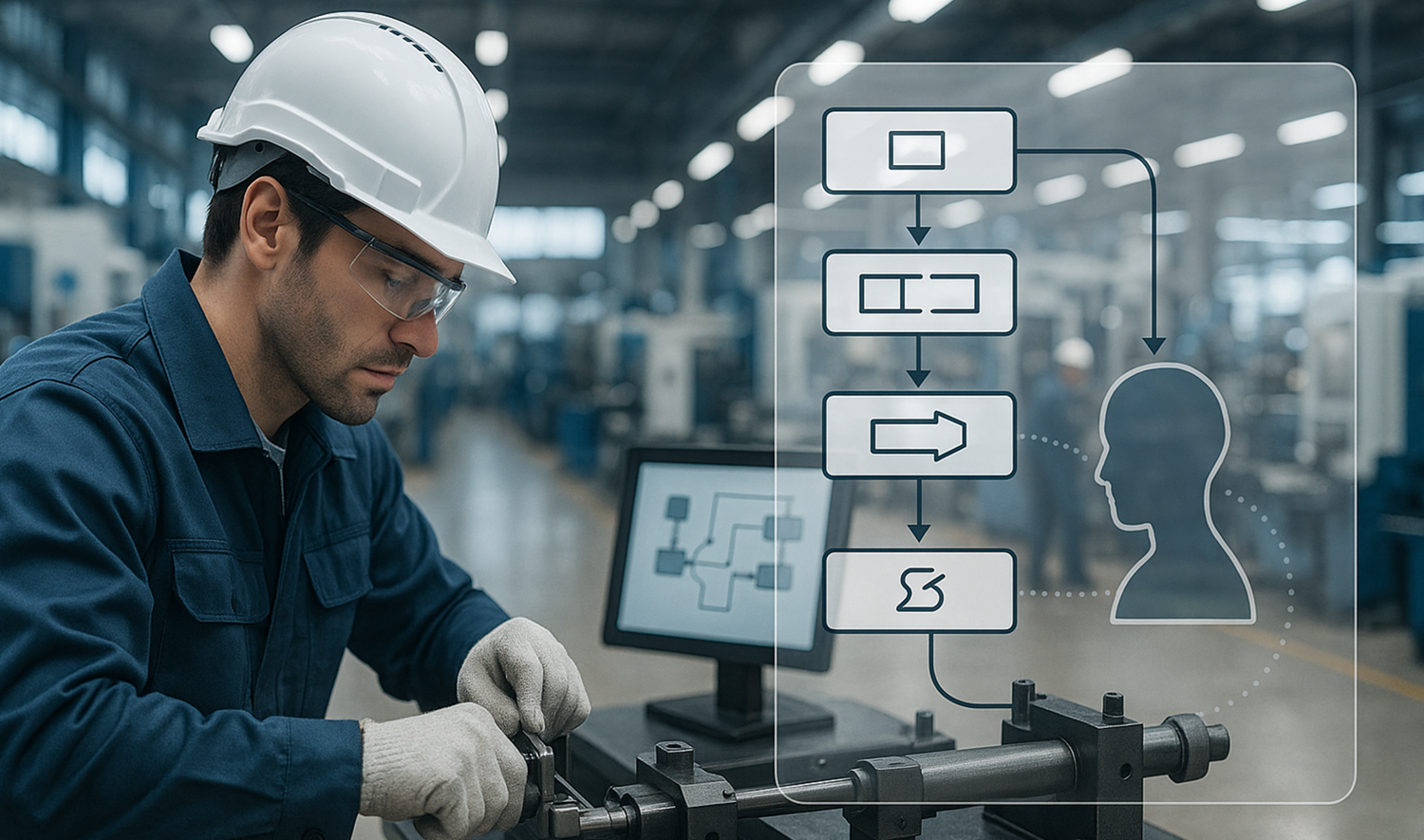
製造業において高品質なマニュアルを作成するためには、作業を適切に分析し、最小単位まで分解することが不可欠です。「熟練者にはできて当たり前」とされる作業の中には、意識されていない判断や動作が多数含まれており、これらを見える化しなければ効果的なマニュアルは作成できません。本記事では、製造現場の作業を最小単位まで分解・分析する具体的な手法と、その結果を効果的にマニュアルに反映させるポイントについて解説します。
作業分析の重要性と効果
1-1. なぜ作業分析が必要か
作業分析には以下のような重要な意義があります。
- 属人化された暗黙知の形式知化
- 効率的な技能伝承の実現
- 品質のばらつき低減
- 改善ポイントの発見
- 効果的な教育訓練の実現
自動車部品メーカーA社では、熟練技能者の作業を詳細に分析したことで、従来「感覚」とされていた判断基準を数値化。これにより新人教育期間を6か月から3か月に短縮できました。
1-2. 作業分析がもたらす効果
適切な作業分析は以下のような効果をもたらします。
- 標準作業の確立
- 効率的な技能伝承
- 作業効率の向上
- 安全性の向上
- 品質向上とコスト削減
作業分析の基本ステップ
効果的な作業分析は以下のステップで進めます。
2-1. 分析対象の選定
分析すべき作業を適切に選定します。
- 品質に影響が大きい工程
- 熟練者と非熟練者で差が出やすい作業
- 不良やトラブルが発生しやすい工程
- 技能伝承が難しいとされる作業
2-2. 分析チームの編成
適切なメンバーで分析チームを編成します。
- 熟練作業者(技能のホルダー)
- 生産技術担当者(分析の専門家)
- 現場管理者(全体視点)
- 必要に応じて品質管理担当者
2-3. 分析の進め方
作業分析は以下の流れで実施します。
- 大まかな工程の把握(フロー作成)
- 各工程の観察と記録(ビデオ撮影が効果的)
- 作業の最小単位への分解
- 各要素作業の分析と整理
- 標準作業としての統合
最小単位作業の洗い出し手法
3-1. 動作分析法
動作を最小単位に分解する代表的な手法です。
- サーブリック分析:基本動作(掴む、運ぶ、置くなど)に分解
- ビデオ撮影による微細動作の可視化
- 動作時間の計測(タイムスタディ)
電子部品メーカーB社では、熟練者の組立作業をハイスピードカメラで撮影・分析し、一見単純に見える「部品の挿入」作業に、「位置合わせ」「角度調整」「押し込み」など5つの微細動作が含まれていることを発見。これらを個別に教育することで、不良率が40%低減しました。
3-2. 判断分析法
作業中の判断プロセスを分析する手法です。
- クリティカルインシデント法:重要な判断場面の抽出
- 発話思考法:作業中に考えていることを声に出してもらう
- インタビュー法:なぜその判断をしたのか詳細に聞き取る
- 比較観察法:熟練者と非熟練者の判断の違いを分析
食品メーカーC社では、熟練検査員に「良品/不良品の判断基準」を詳細にインタビュー。その結果、無意識に「色調」「形状」「触感」の3要素を組み合わせて瞬時に判断していることが判明。これらの判断基準を数値化・言語化することで、検査精度が向上しました。
3-3. 知覚・感覚分析法
五感を使った作業の分析手法です。
- 視覚情報:何をどう見ているか(視線計測など)
- 聴覚情報:音の変化をどう判断しているか
- 触覚情報:触感や力加減の分析(力センサーの活用など)
- 嗅覚・味覚情報:香りや味の判断基準
精密機械メーカーD社では、研磨作業における熟練者の「手加減」を分析するため、グローブ型力センサーを活用。その結果、製品の角度と表面状態に応じて微妙に力を調整していることが判明し、この力加減を数値化・可視化することで技能伝承を実現しました。
作業分析における注意点と対策
4-1. 熟練者特有の課題
熟練者を対象とした分析における課題とその対策です。
- 無意識化した動作:ビデオ撮影とスロー再生による可視化
- 言語化の難しさ:適切な質問と具体的な場面の提示
- 「当たり前」の認識:初心者の視点を取り入れた分析
4-2. 環境・条件の影響
作業環境や条件が分析に与える影響とその対策です。
- 観察による作業の変化:自然な状態での観察の工夫
- 条件によるバラツキ:複数回・複数条件での観察
- 個人差の考慮:複数の熟練者の観察と比較
4-3. 分析の精度と効率のバランス
分析の精度と効率のバランスを取るためのポイントです。
- 目的に応じた分析レベルの設定
- 重要度による分析深度の調整
- 効率的な分析ツールの活用
自動車メーカーE社では、作業の重要度に応じて分析レベルを3段階(簡易分析、標準分析、詳細分析)に分け、リソースの最適配分を実現。これにより、限られた時間内で効果的な作業分析を可能にしました。
分析結果のマニュアルへの反映方法
5-1. 最小単位作業の構造化
分析で得られた最小単位作業を構造化します。
- 階層構造による整理(大工程→中工程→小工程→要素作業)
- 時系列フローによる整理
- 判断と動作の分離整理
- 重要度による分類
5-2. 視覚化テクニック
分析結果を視覚的に表現する方法です。
- 連続写真による動作の表現
- ポイント強調の工夫(矢印、拡大図など)
- 判断フローチャートの活用
- 3D図や分解図の活用
食品機械メーカーF社では、複雑な機械調整作業を「基本的な動作」と「判断ポイント」に分けて整理。基本動作は連続写真で、判断ポイントはフローチャートで表現することで、わかりやすいマニュアルを実現しました。
5-3. 数値化と基準の明確化
感覚的な要素を数値化・基準化する方法です。
- 許容範囲の数値化(〇〇mm±△△)
- 力加減の基準化(〇〇N相当、同等製品との比較など)
- 官能評価の基準サンプル化
- NG/OK事例の視覚化
作業分析の実践事例
6-1. 電子部品製造業での事例
電子部品メーカーG社では、はんだ付け作業の熟練技能者を対象に詳細な作業分析を実施。その結果、「はんだごての当て方」「加熱時間」「はんだ供給タイミング」に熟練者特有のパターンがあることを発見。これらを数値化・可視化したマニュアルを作成したところ、新人の習熟期間が従来の3分の1に短縮され、不良率も60%低減しました。
6-2. 食品製造業での事例
食品メーカーH社では、熟練者の「目利き」による原料選別作業を分析。熟練者の視線計測と判断プロセスのインタビューを組み合わせ、「見るべきポイント」と「判断基準」を明確化。これをマニュアル化し、さらにAI画像認識システムの開発にも活用することで、選別精度の向上と効率化を両立しました。
6-3. 機械加工業での事例
機械加工メーカーI社では、切削加工における熟練者の「異常音の聞き分け」能力を分析。音響分析と熟練者へのインタビューを組み合わせ、正常音と異常音の波形パターンを可視化。これをマニュアル化するとともに、音声認識AIの開発にも活用し、未熟練者でも異常を検知できるシステムを構築しました。
まとめ:作業分析のアクションステップ
効果的な作業分析を実施するためのアクションステップをまとめます。
- 分析対象の選定:重要度と難易度を考慮
- 分析チームの編成:適切な人材の確保
- 観察と記録:ビデオ撮影等による詳細記録
- 作業の分解:最小単位への分解と整理
- 分析と形式知化:暗黙知の可視化と言語化
- マニュアルへの反映:構造化と視覚化
- 検証と改善:現場での試行と継続的な改善
作業分析は一朝一夕で完成するものではありません。分析→マニュアル化→検証→改善のサイクルを回しながら、徐々に精度を高めていくことが重要です。本記事で紹介した手法を活用し、貴社の製造現場に適した作業分析とマニュアル作成に取り組んでみてください。
この記事を書いた人
編集部