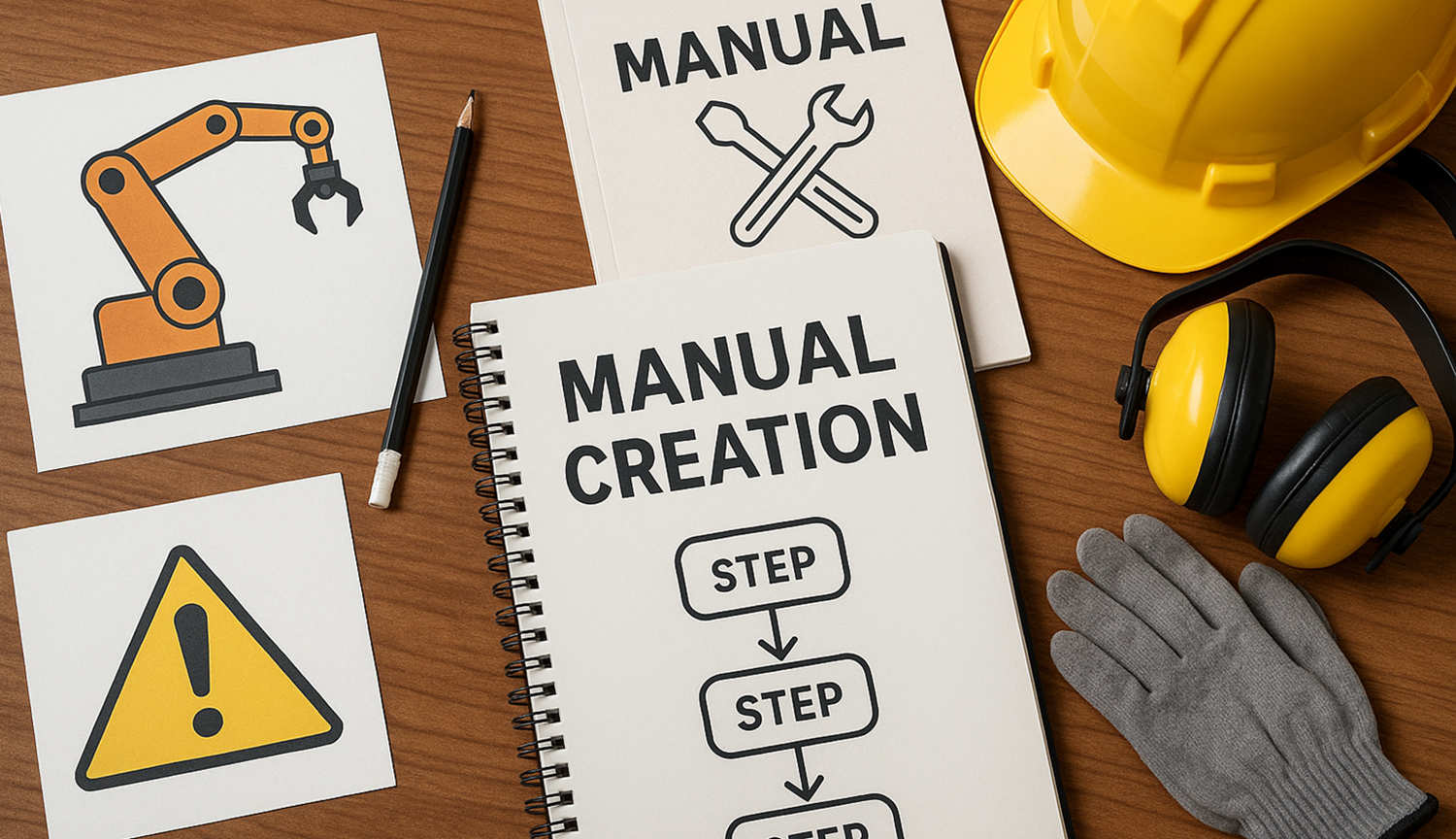
製造業において、品質の安定と作業の標準化はビジネスの根幹を支える重要な要素です。その実現に欠かせないのが、適切に設計された作業マニュアルです。しかし、「作ったはいいが誰も見ない」「内容が現場と乖離している」といった課題を抱えている企業も少なくありません。本記事では、製造現場で本当に活用される効果的なマニュアル作成のポイントを、準備から運用までの流れに沿って解説します。
目次
マニュアル作成の重要性と基本原則
製造業におけるマニュアルは単なる作業手順書ではなく、以下の価値を持つ重要なツールです。
- 品質の安定化と不良率低減
- 作業の標準化による生産性向上
- 新人教育・技能伝承の効率化
- 属人化防止とリスク分散
- コンプライアンスと安全管理の徹底
効果的なマニュアルを作成するための基本原則は「正確性」「簡潔性」「視認性」「実用性」の4つです。これらのバランスを取りながら作成することが重要です。
作成前の準備:目的と対象を明確に
2-1. 目的の明確化
マニュアル作成の第一歩は、「なぜ作るのか」「何を達成したいのか」を明確にすることです。
- 新人教育用なのか
- 熟練者の作業標準化なのか
- 品質トラブル対策なのか
- 安全管理強化なのか
目的によって内容や構成、詳細度が変わることを認識しましょう。
2-2. 対象読者の特定
対象読者の知識レベルや経験値を把握することが重要です。
- 未経験者向け:基本用語の解説から詳細なステップ説明
- 経験者向け:重要ポイントの強調とトラブル対応
- 多国籍作業者向け:言語の簡略化、視覚情報の強化
2-3. 現場観察とプロセス分析
実際の作業を観察・記録し、工程を細分化しましょう。このとき以下の点に注意します。
- 熟練者と初心者の作業比較
- ボトルネックや難所の特定
- 品質に影響する重要工程の抽出
- 安全面でのリスクポイント
製造現場特有のマニュアルに入れるべきポイント
3-1. 安全性の確保
製造現場では安全が最優先事項です。
- 危険箇所や作業の明示(警告マークの活用)
- 保護具の着用タイミングと正しい使用法
- 緊急時の対応手順
- 「なぜその手順が必要か」の理由説明
3-2. 品質管理の視点
品質管理ポイントを明確に示すことで不良発生を防止します。
- 検査項目と基準値の明示
- NG/OK事例の視覚的表示
- トレーサビリティ記録方法
- 品質異常時の対応フロー
3-3. 設備・治具の正しい使用法
製造設備や専用治具の扱いは製品品質に直結します。
- 設備の正しい操作手順
- 調整・段取り替えのポイント
- 日常点検項目と頻度
- トラブル発生時の初期対応
効果的な構成と表現方法
4-1. 構成の基本
読みやすく実用的なマニュアルの基本構成は、以下のようになっていることが多いです。
- 目的と概要
- 必要な工具・材料・設備
- 安全上の注意点
- 準備作業
- 本作業(順を追った手順)
- 検査・確認項目
- トラブルシューティング
- 関連資料・問い合わせ先
4-2. 視覚情報の効果的活用
文字情報だけでなく、視覚情報を効果的に活用しましょう。
- 実際の作業写真(ポイントを矢印や囲みで強調)
- 工程フロー図
- 3D/分解図(必要に応じて)
- 色分けによる重要度の表示
4-3. 表現の工夫
理解しやすい表現を心がけましょう。
- 一文一動作の原則
- 命令形での明確な指示(「~する」)
- 専門用語は初出時に解説
- 数値の明確な表示(「少し」ではなく「5mm程度」など)
マニュアルの評価と改善サイクル
作成したマニュアルは「作って終わり」ではなく、現場での検証と継続的な改善を通じて、初めて実用性を持ちます。
5-1. 初期評価の実施
運用前には、以下のようなステップでマニュアルの有効性を確認しましょう。
- 初心者による実践テスト:説明通りに作業が進められるかを検証
- 熟練者によるレビュー:記載の抜け・誤り・非効率な表現の指摘
- 現場責任者による承認:安全・品質基準を満たしているかの最終チェック
5-2. 定期的な見直しと更新
マニュアルは「静的な文書」ではなく、現場の変化とともに進化する“生きたツール”です。例えば以下のような運用を取り入れ、継続的な見直し体制を整えましょう。
- 工程や設備の変更があった場合は、暫定手順を即時発行し、正式マニュアルには1週間以内に反映するルールを設ける
- 現場リーダーが週1回の「簡易マニュアル点検」を実施し、「読みづらい」「実情と合わない」といった意見を現場で拾い上げる
- 作業者への口頭ヒアリング+簡易アンケートを併用することで、経験年数による温度差のあるフィードバックを偏りなく集める
- 半期ごとに旧版との比較を実施。管理部門での承認と記録管理まで行う
など
現場への定着化と活用促進
マニュアルの品質がいかに高くても、実際に現場で使われなければ意味がありません。運用段階では「アクセスのしやすさ」と「使う動機づけ」の両方を仕組みとして設計することがポイントです。
6-1. アクセス性と使いやすさの工夫例
- 紙媒体だけでなく、「1ページ1作業」形式の小分けラミネートを作成し、作業台に吊り下げる方式にすると、必要な部分だけをすぐ参照できる
- スマートフォンや現場用タブレット端末から、QRコードでマニュアル動画へ直接アクセスできる仕組みを用意
- 使用頻度が低い手順ほど“検索性”が重要になるため、電子ファイルには「手順番号検索機能」や「タグ分類」を導入
- 図や写真中心の「瞬間理解型マニュアル」(3秒で理解できる)を掲示用に別途作成するケースも効果的
6-2. 運用を根づかせる仕掛けと仕組み
- マニュアルを用いた実地訓練後に、必ず現場フィードバックを収集し、その声を翌月のマニュアル改善に反映(フィードバック→改善の習慣化)
- 「マニュアル活用シート」を作業者が毎回記入する運用を設け、どの作業で何を参考にしたかを記録
- 作業者主導でマニュアルを更新・提案する場を定期的に設け、形式だけでなく中身にも参加してもらう
- 活用率や改善提案件数を可視化し、部門単位で共有。活用率の高いチームには「現場標準推進賞」などを設け、継続的な動機づけに
業種別の成功事例
7-1. 自動車部品製造業A社の事例
A社では、多言語対応の写真中心マニュアルを導入し、外国人作業者の教育時間を従来の1/3に短縮。不良率も5%から1%未満に改善しました。
7-2. 食品製造業B社の事例
B社では、衛生管理と品質管理を一体化したマニュアルシステムを構築。タブレット端末での記録と連動させることで、作業と同時に品質記録が完了する仕組みを実現し、生産性が15%向上しました。
まとめ:「現場で活きるマニュアル」はつくり方で決まる
製造業におけるマニュアルは、単なる作業手順書ではなく、現場の安全と品質、教育効率を支える“仕組み”です。そのためには、作成時点での工夫と、運用・改善を視野に入れた設計が不可欠です。
とくに以下の点は、現場に根差したマニュアルをつくるうえでの鍵となります。
- 机上で完結させず、現場の声を起点に作る
- 視覚情報や言語表現を工夫し、多様な作業者に配慮する
- 更新しやすく、浸透しやすい形態で提供する
- 安全・品質・教育のバランスを常に意識する
マニュアルは一度作って終わりではなく、製造現場とともに「育てていく」ものです。形式やフォーマットにとらわれすぎず、現場で“見られ、使われ、役立つ”ことを第一に据えて取り組むことが、失敗しないマニュアル作成の第一歩となるでしょう。
この記事を書いた人
編集部