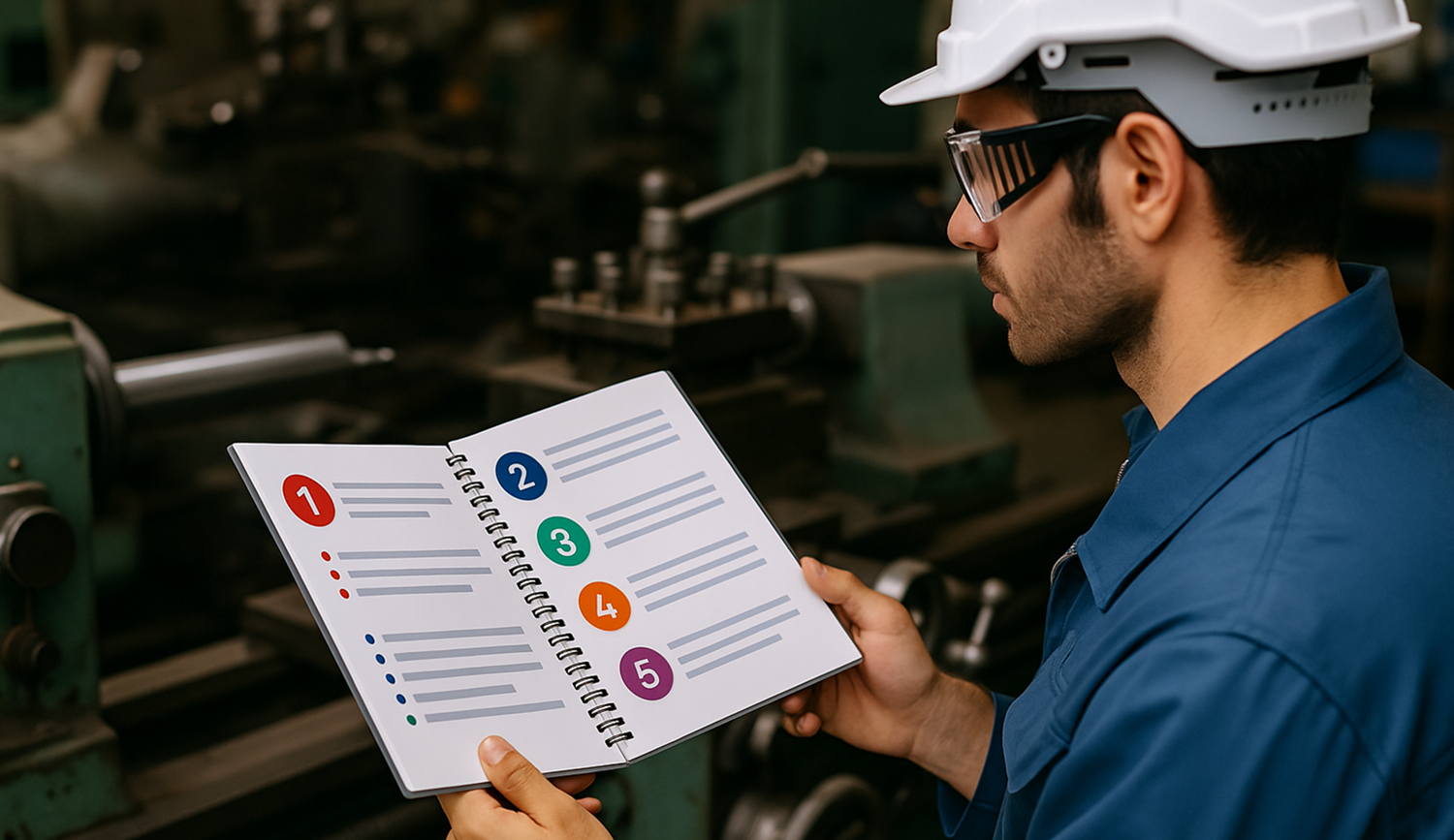
製造現場において、安定した品質の製品を効率的に生産するためには、標準化された作業手順が不可欠です。しかし、多くの企業では「作成したマニュアルが現場で使われない」「内容が現場の実態と乖離している」といった課題を抱えています。本記事では、実際に現場で活用される効果的な製造マニュアルを作成するための5つの重要ポイントを、具体的な事例とともに解説します。
マニュアル作成の目的と対象者を明確にする
マニュアル作成でまず押さえるべきは、「何のために」「誰のために」作るのかという点です。
1-1. 目的の明確化
製造マニュアルの作成目的には様々なものがあります。
- 新人教育の効率化
- 熟練者の暗黙知の形式知化
- 品質トラブルの再発防止
- 安全性の向上
- ISO等の認証対応
目的によって、マニュアルの内容や構成、詳細度が変わってきます。例えば、新人教育用であれば基礎知識から丁寧に解説する必要がありますが、熟練者向けのトラブル対応マニュアルであれば、要点を簡潔にまとめることが重要です。
1-2. 対象者の特性把握
対象者の知識レベルや経験、言語能力などを考慮することも重要です。
- 未経験者:基礎用語の解説から
- 中堅作業者:重要ポイントとトラブル対応に重点
- 外国人作業者:言語の簡略化と視覚情報の強化
現場の実態を正確に把握する
効果的なマニュアル作成には、現場の実態把握が欠かせません。
2-1. 作業観察とプロセス分析
現場での実際の作業を観察し、以下の点を把握しましょう。
- 熟練者と初心者の作業の違い
- 作業の手順とタイミング
- 使用する工具・設備の扱い方
- 判断を要するポイント
重要なのは、公式の手順と現場での実際の作業にズレがないかを確認することです。現場では「正式な手順より効率的なやり方」が存在していることも少なくありません。それが品質や安全性を損なわないものであれば、マニュアルに反映するべきでしょう。
2-2. 属人化ポイントの洗い出し
特に注意すべきは、「この人でないとできない」という属人化された作業です。
- 経験や勘に頼る判断基準
- 微妙な力加減や感覚的な調整
- 暗黙知となっている判断基準
電子部品メーカーC社では、熟練者のはんだ付け作業を高速カメラで撮影・分析し、「良品と不良品の違いが出る微妙な手の動き」を数値化することで、属人化していた技能を標準化することに成功しました。
安全と品質を確保する情報設計
製造マニュアルにおいて、安全確保と品質保証は最重要事項です。
3-1. 安全情報の明示
- 危険度に応じた警告表示(「危険」「警告」「注意」の区分)
- 保護具の着用タイミングと正しい使用法
- 危険作業の前後に注意喚起
- 「なぜその手順が必要か」の理由説明
化学製品メーカーD社では、すべての作業手順書に「この手順を守らなかった場合のリスク」を明記することで、安全意識の向上と規則遵守率の向上を実現しました。
3-2. 品質管理ポイントの明確化
- 重要管理項目と許容範囲の明示
- 検査方法と判定基準の具体化
- NG/OK事例の視覚的表示
- 異常時の対応手順
視覚情報を効果的に活用する
文字情報だけでなく、視覚情報を効果的に活用することで、マニュアルの理解度と実用性が大きく向上します。
4-1. 写真・イラストの活用法
- 実際の作業写真にポイントを矢印で示す
- 連続写真による動作の表現
- NG/OK事例の比較写真
- 3D/分解図による立体的な把握
自動車部品メーカーE社では、従来の文字中心マニュアルから写真中心マニュアルに変更した結果、新人の習熟時間が30%短縮され、初期不良率も半減しました。
4-2. 図解・記号の標準化
社内で使用する図解や記号を標準化することで、マニュアル間の一貫性を保ち、理解しやすさを向上させます。
- 危険レベルを示す警告マーク
- 作業の種類を示すアイコン
- 品質チェックポイントを示す記号
- 時間・個数などの単位表記
4-3. レイアウトの工夫
情報の優先度に応じたレイアウト設計も重要です。
- 重要情報の強調(色・フォントサイズ)
- 関連情報のグルーピング
- 手順の流れに沿った配置
- 余白を適切に取り視認性確保
継続的な改善と定着化のしくみづくり
マニュアルは作って終わりではなく、継続的に改善し、現場に定着させることが重要です。
5-1. 評価と改善のサイクル
- 初期評価:初心者による実践テスト
- 定期的な見直し:3〜6ヶ月ごと
- 改善提案の仕組み:現場からのフィードバック収集
- 製品・工程変更時の即時更新
食品メーカーF社では、マニュアルの各ページに「改善提案QRコード」を設置。スマートフォンで読み取るとその場で改善提案が送信できる仕組みを導入し、年間200件以上の改善提案が寄せられるようになりました。
5-2. 現場への定着化策
せっかく良いマニュアルを作成しても、活用されなければ意味がありません。
- アクセシビリティの確保:作業場所近くへの配置
- 教育訓練への組み込み:OJT時の活用
- 改善活動との連携:小集団活動での活用
- 成功体験の共有:マニュアル活用による成功事例の紹介
精密機器メーカーG社では、タブレット端末を各工程に配置し、作業者がいつでも最新のマニュアルを参照できるようにするとともに、作業実績データと連動させることで、マニュアル遵守率と製品品質の相関を「見える化」しました。これにより、マニュアル遵守の重要性が現場に浸透し、不良率が大幅に低減しました。
まとめ:実践のためのステップ
効果的な製造マニュアルを作成・活用するための5つのポイントを実践するためのステップをまとめます。
- マニュアルの目的と対象者を明確にし、文書化する
- 現場観察と工程分析を丁寧に行い、属人化ポイントを洗い出す
- 安全と品質を確保するための重要情報を優先的に盛り込む
- 視覚情報を効果的に活用し、理解しやすさを向上させる
- 継続的な改善と定着化のサイクルを確立する
製造マニュアルは「生きた文書」であり、現場と一体となって進化させていくことが重要です。本記事で紹介した5つのポイントを押さえることで、現場で本当に活用される効果的なマニュアル作成に取り組んでいただければ幸いです。
この記事を書いた人
編集部