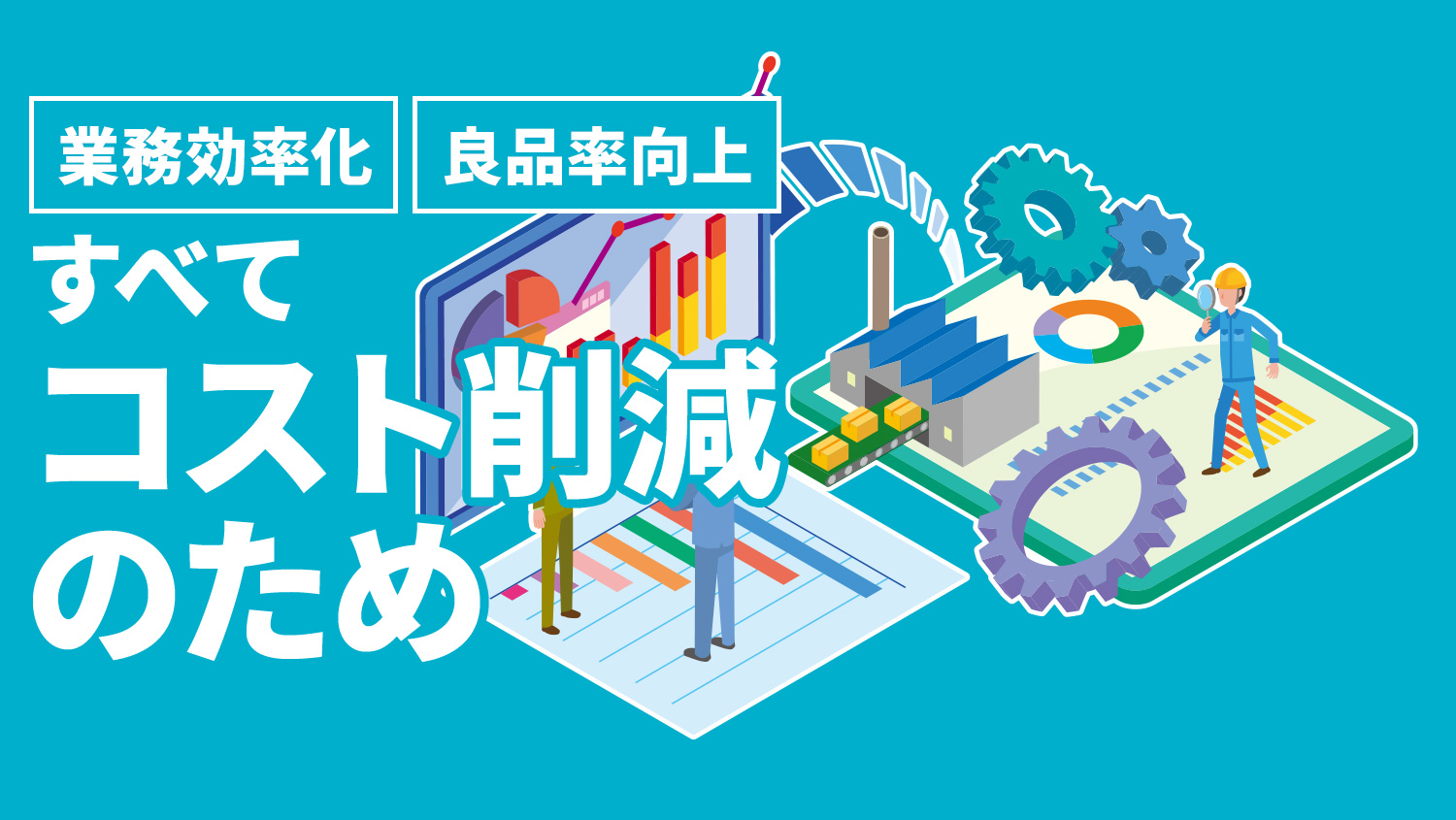
コスト削減は最重要課題
⽣産現場に従事する⽅々は、業務効率化や良品率向上といった⽇々の改善活動に取り組んでいます。これらはすべてコスト削減を⽬的としており、安く、早く、⾼品質なものを安定して⽣産することが、会社にとって⼤きな利益をもたらします。
原価が下がり、販売価格を下げることができれば、お客様は安い製品を多く買ってくれます。原価が下がっても販売価格を下げない場合、コスト削減した分はそのまま会社の儲けとなり、設備投資や従業員の給与アップにつなげてくれるかもしれません。
社員一人一人が利益確保のために努⼒し、コツコツとコスト削減の成果をあげることができれば、会社や社員の⽣活が潤うのです。コスト削減は会社のためでもあり、家族のためでもある。そう思うことができれば、これまで以上に熱意をもってコスト削減に取り組むことができるでしょう。
現状は決してベストな状態ではない
コスト削減と⾔われても、具体的な⼿法がわからない。実はこれ、とてもありがちな悩みです。前任者から引き継いだ仕事だったり、⾃分より知識をもっている⼈が決めた仕事だから、現状がもっとも良い状態になっていると思ってしまうかもしれません。
しかし、そんなことはありません。改善⼿法によって難易度の違いはありますが、必ず今よりも良い状態にすることはできます。そのような⽬線で現場を⾒直せば、コスト削減の⽷⼝は必ず⾒つかります。
コスト削減は⾝近なところから
3M(ムリ・ムダ・ムラ)という⾔葉を聞いたことはあるでしょうか。
3Mは負荷と能⼒の最適バランスを図るために、排除しなければならない状況を指した⾔葉ですが、よりわかりやすく⾔い換えると、効率を上げるために取り除くべき3つのワードということになります。
コスト削減においてもっとも⼤きく影響するのは『ムダ』であり、ムダはどのような仕事にも必ず存在します。しかし、作業者の慣れや気付きの不⾜により、ムダは作業の中に紛れ込みやすい性質をもっており、100%排除するのは⾮常に困難です。
もうひとつ、3R(リデュース・リユース・リサイクル)という⾔葉があります。
3Rは⽣産における材料や廃棄物の量を少なくする取り組みのことを指しますが、3Rでは『リユース』と『リサイクル』がコスト削減のヒントとなります。製品を洗浄して使い回す、使い回せるものを作る、廃棄物を材料として再⽣する……といった活動が3Rの⾔葉から⾒えてきます。
このように、世の中にある⾔葉を現場に落とし込むだけでもヒントを得ることができます。
コスト削減のネタは⾝近にたくさんあり、すぐに検討を始めることができます。その中でも特にムダ、リユース、リサイクルの3つはコスト削減の⼤きなキーワードとなります。
ただ、そう⾔われてもなかなか具体的なアイデアに落とし込めない、もっと具体的な事例を知りたい、という⽅に向けて、今回は実際のコスト削減事例を交えて紹介していきますので、現場に活⽤できることを探してみてください。現場や作業内容を⾒直すヒントが必ず⾒つかるはずです。
コスト削減に取り組む前に
コスト削減に着⼿する前に、必ず⾏うべきこと。それは現状分析と予想効果の試算です。
家計を⾒直す第⼀歩は家計簿をつけることと⾔われますが、それはお⾦のムダ遣いを⾒極めるためであります。製造現場でも同様です。製品原価のすべてを理解する必要はありませんが、材料費と加⼯費の内訳だけでも知っておくべきでしょう。
そして、削減⽅法はできるだけ2つ以上提案することも⼤切です。思いつきの⽅法にすぐ着⼿するよりも、検討期間を設けて短期間で⼤きな効果を⾒込める⽅法を探りましょう。実現性と予想効果から優先順位を明確化することがコスト削減の第⼀歩となります。
事例
コスト削減事例[1] 材料梱包を変更
A社で購⼊している材料はダンボールで梱包され⼊荷していましたが、材料は輸送中に破損しないよう、⼤量の緩衝材が使われていました。材料業者はさまざまな顧客に材料を販売しているため、納品距離の近いA社向けの製品でも遠⽅へ輸送する場合と同じ梱包⽅法をとっていました。
そのため、A社にとっては過剰梱包はムダとなっていました。A社は材料業者と協議し、ダンボールを廃⽌し、通い箱を⽤意しました。また、都度廃棄していた緩衝材はウレタン製の使い回しが効くものに変更しました。
このようにしてリユース化を⾏い、材料の購⼊費⽤を削減しました。また、緩衝材の⽚付けや、廃棄作業が不要となったことで作業⼯数が削減されました。
コスト削減事例[2] ⽣産サイクルの向上
B社では、製品ひとつ当たりの⽣産に120秒かかっていました。120秒の内訳は、90秒が機械による加⼯、30秒が⼈の作業です。
機械加⼯の速度を向上させることは可能でしたが、⽣産速度と引き換えに不良品が多発する可能性があることから、⼈の作業を短縮させる⽅がリスクが少ないと考え、検討を⾏いました。作業者に聞き取りを⾏ったところ、部品同⼠のはめ込み位置が⽬視で確認しづらいため作業に時間がかかっていることがわかり、治⼯具で補助することにより⼯数を半減させることができました。
⼈の作業という点は変わりませんが、作業効率を⼤幅に上昇させてコスト削減を実現させた事例です。
コスト削減事例[3] 不良率の改善
C社では顧客から要求されている製品規格を確実に満たすため、社内的な規格を厳しく設定していました。
あるとき、コスト⾒直しのために不良率を分析したところ、主な不良原因は社内規格を満たしていないという理由でした。しかし、検査結果を確認すると顧客の要求規格内に収まっていたのです。つまり、過剰な品質を保つために本来良品である製品を廃棄していたということになります。
そこで、社内会議を経て社内規格を⾒直し、顧客の要求規格に近い値に⾒直したことで、⼤幅に不良率が改善されました。製品の出来栄えは変えず、過剰な規格値を⾒直すことによってコスト削減を⾏うことも可能という事例です。
⾒えるコストと⾒えないコスト
コストには⼤きく分けて『⾒えるコスト』と『⾒えないコスト』の2種類があります。
上記で事例を交えて紹介してきたのは⾒えるコストです。それに対して、⾒えないコストとは、わかりやすい事例でいえば社員同⼠の雑談や会議の時間、社内を移動する時間、部下を管理・指導するための時間、ファイルやデータを探す時間など、普段の何気ない時間が⾒えないコストの代表です。削減は難しいものの、確実に⼈件費がかかっているのです。
⾒えないコストを削減するには
前述の通り、時間的なロスが⾒えないコストの主要因です。つまり、⼈の動線を⼯夫したり、ファイルを整理して必要なときにすぐ取り出せる状態にしたり、指導の時間を効率化するといったムダの排除が有効な⼿段となります。
時間を有効活⽤するための環境整備がカギとなります。⾒えないコストの削減⼿法としては、マニュアルを⼀元管理するサービスを⽤いることも有効です。
マニュアル一元管理にお悩みの方はこちらのサービスをご覧ください。
コスト削減の重要性と考え⽅
本記事では事例を交えながらコスト削減の⼿法をご紹介しました。
コスト削減とは、⾒える・⾒えないにかかわらず、ムダな材料や時間を顕在化・分析し、削減⼿法を考え、優先順位をつけて推進することです。
コストの削減によって会社の業績向上につながれば、従業員へのリターンにつながります。
それは給料や、会社の存続など、さまざまな形で現れますが、意味は必ずあります。
⾝近に散りばめられているコスト削減のきっかけを拾い上げ、検討し、効果的なプランを練り上げて実⾏しましょう。
この記事を書いた人
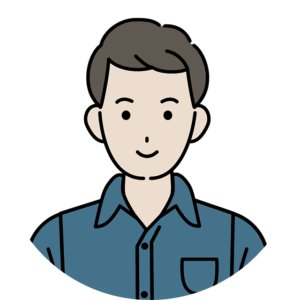
みだん
製造業に製品検査、品質管理で15年以上従事する副業ライター。 2度の離婚、注文住宅を3度建てるなど波乱の人生を歩む。 3度目の結婚にてパートナーに恵まれ、最近生まれたばかりの子供にメロメロ。 趣味は浅く広いサブカル全般と国内旅行と子供の世話。 執筆歴は長いが副業として始めたのは極々最近。 得意ジャンルは製造業関連の他、アニメ・ゲーム・映画などのサブカルチャー、注文住宅、男女の恋愛観。