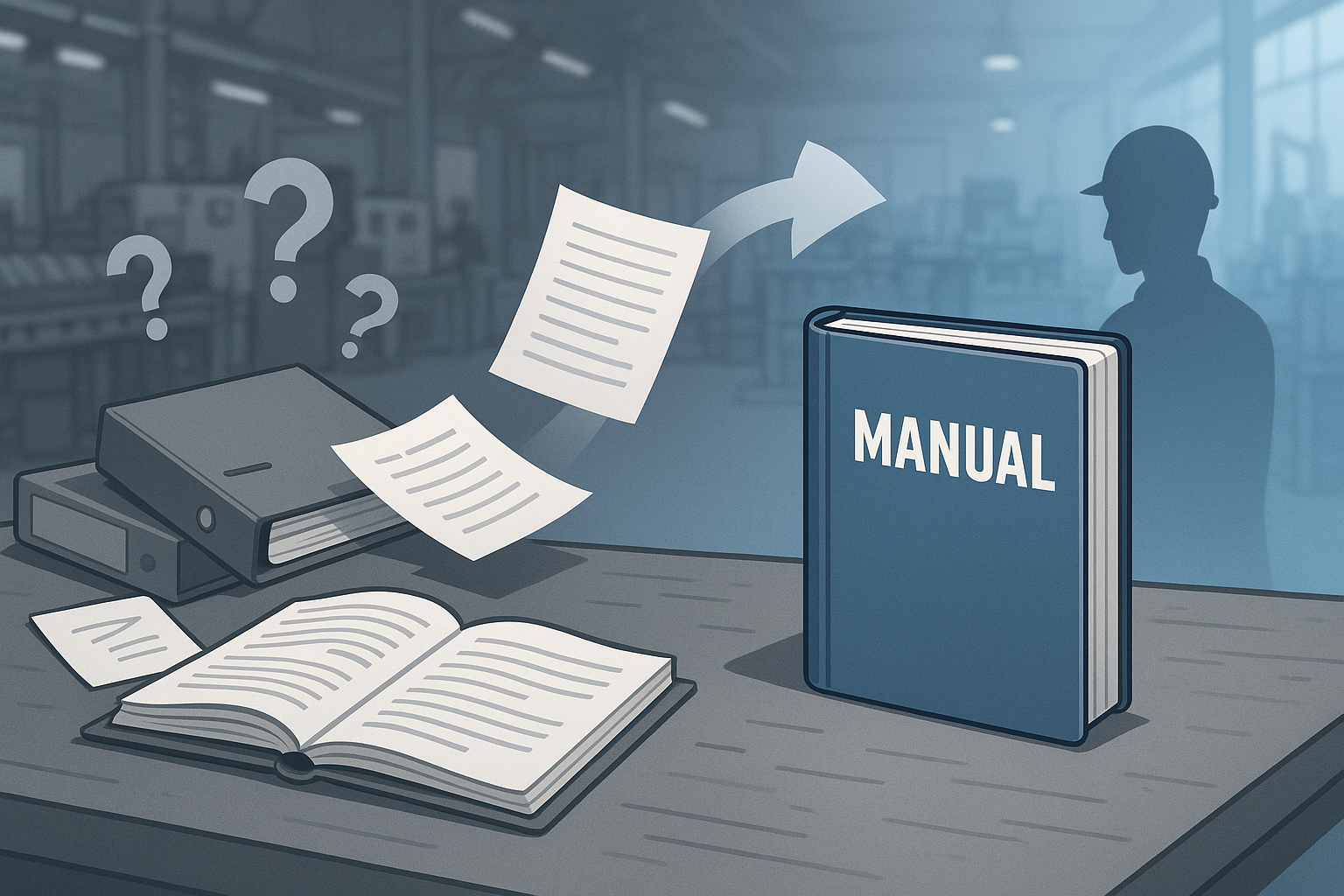
製造業において、作業手順書やマニュアルは品質の安定化や技能伝承において不可欠なツールです。しかし、「作ったのに誰も見ない」「使いにくい」というマニュアルも少なくありません。本記事では、製造現場でよく見られるマニュアル作成の失敗パターンと、それを回避するための具体的な方法を解説します。マニュアル作成担当者の皆さまが陥りがちな落とし穴を知り、より効果的なマニュアル作成に役立てていただければ幸いです。
目次
失敗①:現場の実態を反映していない
問題点
机上で作成されたマニュアルが、実際の現場作業と乖離していることがあります。
- 「理想的な手順」と「実際の作業」のギャップ
- 現場の制約条件(スペース、治具など)が考慮されていない
- 熟練者の暗黙知が反映されていない
回避法
- 現場での実際の作業観察を徹底する
- 熟練者へのインタビューと作業分析を実施する
- マニュアル案を現場でトライアルし、フィードバックを得る
自動車部品メーカーA社では、マニュアル作成前に「作業観察シート」を作成し、熟練者の作業を複数回観察・記録することを必須としました。この取り組みにより、従来見落とされていた暗黙知が明らかになり、より実践的なマニュアルが完成しました。
失敗②:読み手を考慮していない
問題点
マニュアルの対象読者が明確でなく、どのレベルの人に向けて書くかが不明確です。
- 新人には難しすぎる専門用語の使用
- 経験者には冗長すぎる基本説明
- 外国人作業者の言語障壁への配慮不足
回避法
- 対象読者を明確に設定する(新人、中堅、多国籍など)
- 対象に合わせて専門用語の解説や図解を調整する
- 必要に応じて複数バージョンを用意する(簡易版/詳細版など)
電子部品メーカーB社では、マニュアルを「初級編(新人向け)」「標準編(一般作業者向け)」「応用編(トラブル対応含む)」の3段階に分け、QRコードで相互リンクさせるアプローチを採用。作業者の習熟度に合わせた情報提供が可能になりました。
失敗③:文字情報が多すぎる
問題点
文字だらけのマニュアルは読みにくく、重要ポイントも伝わりにくくなります。
- 長文の説明が続き読む気が失せる
- 視覚的な理解が必要な作業が言葉だけで説明されている
- 探したい情報を見つけにくい
回避法
- 「文字:視覚情報」の比率を「3:7」程度に抑える
- 重要ポイントは写真や図解で視覚化する
- 複雑な動作は連続写真や動画(QRリンク)で示す
電機メーカーC社では、従来の文字中心マニュアルを全面的に見直し、写真中心・最小限のテキストという原則でリニューアル。その結果、特に外国人作業者の理解度が向上し、品質問題が40%減少しました。
失敗④:曖昧な表現が多い
問題点
曖昧な表現は人によって解釈が異なり、作業のばらつきを生みます。
- 「適量」「しっかりと」「十分に」などの主観的表現
- 具体的な数値や判断基準の欠如
- 複数の動作をひとまとめにした表現
回避法
- 曖昧な表現を具体的な数値に置き換える
- 一文一動作の原則で記載する
- NG/OK事例を視覚的に示す
食品メーカーD社では、調理工程の「適量」「程よく」などの表現をすべて数値化(「5g±0.5g」など)。同時に計量器具も導入したところ、製品の味のばらつきが大幅に減少し、クレームが前年比60%減少しました。
失敗⑤:重要ポイントが埋もれている
問題点
マニュアル全体の中で、特に重要なポイントが強調されていません。
- すべての情報が同じ重みで書かれている
- 品質や安全に関わる重要ポイントが目立たない
- 「必ず守るべきこと」と「参考情報」の区別がつかない
回避法
- 重要度に応じた視覚的階層付け(色分け、枠囲み等)
- 「重要」「必須」などのアイコン活用
- チェックポイントの明確な表示
精密機器メーカーE社では、マニュアル内の情報を「必須(赤枠)」「重要(黄枠)」「参考(灰色背景)」の3段階で視覚的に区分けするフォーマットを導入。作業者が優先すべきポイントが一目でわかるようになり、重要工程の遵守率が向上しました。
失敗⑥:「なぜそうするのか」の説明がない
問題点
手順だけが示され、その理由や背景が説明されていません。
- 作業の意義が伝わらず、モチベーションが低下
- 例外的状況での判断ができない
- 改善提案が生まれにくい環境になる
回避法
- 重要な手順には「理由」を簡潔に添える
- QC工程表と連動させ、品質特性との関連を示す
- 守らなかった場合の影響・リスクを明示する
自動車メーカーF社では、各作業手順に「この工程が品質に与える影響」を明記するフォーマットに変更。作業者の理解度が向上し、自主的な品質チェックの意識が高まりました。
失敗⑦:安全情報の記載が不十分
問題点
安全に関する情報が不足していたり、形式的な記載にとどまっています。
- 一般的な注意事項のみで具体性がない
- 手順とは別の場所にまとめて記載され見落とされやすい
- リスクの程度や回避方法が不明確
回避法
- 関連する作業手順の直前に安全情報を配置
- 危険度に応じた表現の使い分け(「危険」「警告」「注意」)
- 具体的な危険内容と保護方法の明示
化学メーカーG社では、作業手順書の安全情報に「理由」と「保護方法」を明記する形式に変更。「なぜその安全対策が必要か」を理解することで保護具着用率が向上し、労働災害が大幅に減少しました。
失敗⑧:更新・メンテナンスの仕組みがない
問題点
一度作成したマニュアルが更新されず、現場の実態と乖離していきます。
- 設備や材料の変更がマニュアルに反映されない
- 改善活動の成果が盛り込まれない
- 古いマニュアルが現場に残り混乱を招く
回避法
- 定期的なレビューと更新の仕組みを構築する
- 改訂履歴の明確な管理
- 現場からのフィードバック収集の仕組み化
電子部品メーカーH社では、各作業マニュアルにQRコードを設置。スマートフォンで読み取ると「改善提案フォーム」が開き、その場で意見を送信できる仕組みを構築。年間200件以上の改善提案が集まり、マニュアルの進化を促進しています。
失敗⑨:マニュアルの場所や探しやすさが考慮されていない
問題点
必要な時にマニュアルを参照できない状況が発生しています。
- 作業場から離れた場所に保管されている
- 膨大なファイルの中から必要な情報を探すのが困難
- 汚れや破損で読みにくくなっている
回避法
- 作業場所の近くに配置する
- インデックスや見出しの工夫
- 耐久性のある形態(ラミネート加工など)
- デジタル化とQRコード活用
機械メーカーI社では、作業現場の各ステーションにタブレット端末を設置し、デジタルマニュアルをいつでも参照できる環境を構築。また、各設備にQRコードを貼り付け、スキャンするとその設備のマニュアルがすぐに表示される仕組みも導入しました。
失敗⑩:現場への浸透策が講じられていない
問題点
マニュアルを作成しても、現場への浸透施策が不足しています。
- マニュアルの存在や更新が周知されていない
- 使い方の教育がなされていない
- 遵守状況の確認がない
回避法
- マニュアル活用を前提とした教育訓練の実施
- 朝礼や定例ミーティングでの周知
- 遵守状況の定期的な確認と指導
- マニュアル活用の効果の見える化
食品メーカーJ社では、改訂したマニュアルの導入時に「マニュアル説明会」を開催し、変更点の理由と効果を丁寧に説明。また、「マニュアル遵守月間」を設け、現場リーダーによる確認と指導を強化したところ、短期間でマニュアルが定着し、品質指標が改善しました。
まとめ:効果的なマニュアル作成のためのアクションステップ
以上の失敗を回避し、効果的なマニュアルを作成するためのアクションステップをまとめます。
- 現場観察と作業分析を徹底する
- 対象読者を明確にし、そのニーズに合ったマニュアルを設計する
- 視覚情報と文字情報のバランスを取り、見やすさを確保する
- 曖昧な表現を排除し、具体的な数値や基準を明示する
- 重要ポイントを視覚的に強調する工夫を取り入れる
- 「なぜそうするのか」の理由や背景を簡潔に説明する
- 安全情報を適切な場所に効果的に記載する
- 定期的な見直しと更新の仕組みを構築する
- マニュアルの配置と探しやすさを工夫する
- 現場への浸透策を計画的に実施する
マニュアルは「作って終わり」ではなく、継続的に改善し、現場で活用される状態を維持することが重要です。本記事で紹介した失敗パターンと回避法を参考に、より効果的なマニュアル作りにチャレンジしてみてください。
この記事を書いた人
編集部