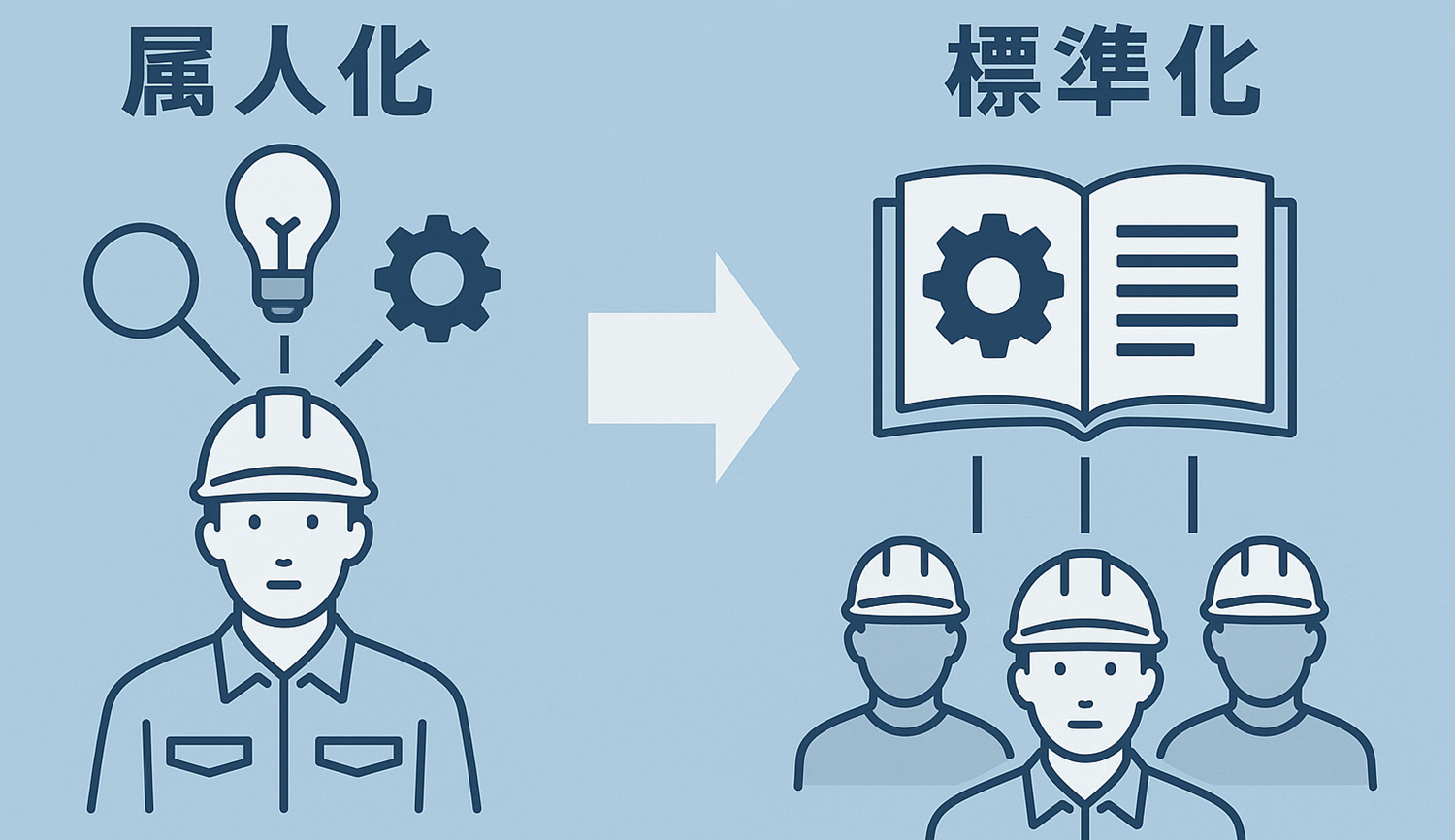
製造業において「この人しかできない」という状況は、品質の安定性やビジネスの継続性を脅かす大きなリスクです。特に熟練技能者の退職や突然の欠勤が生じた際に、生産に支障をきたすケースは少なくありません。本記事では、技能の属人化を防ぎ、誰が作業しても同じ品質を実現するためのマニュアル作成術について、具体的な方法と事例を交えて解説します。
目次
属人化とは何か:製造現場での属人化の実態と課題
属人化とは、特定の個人の経験やスキルに依存した状態を指します。製造現場ではこのような状況が多く見られます。
1-1. 製造現場における属人化の典型例
- 熟練者の「勘」や「コツ」に頼った調整作業
- 文書化されていない判断基準
- 経験に基づく異常検知と対応
- 特定の人しか使いこなせない専用工具や設備
1-2. 属人化がもたらすリスク
属人化は以下のような様々なリスクをもたらします。
- 品質のばらつき
- 生産の不安定化(特定の人が休むと生産できない)
- 技術伝承の困難
- 改善活動の停滞
- 人材配置の硬直化
特に人手不足が深刻化する中、属人化の解消は製造業の喫緊の課題となっています。
属人化を防ぐマニュアル作成の準備段階
効果的なマニュアル作成の準備段階では、以下のステップが重要です。
2-1. 現状分析:属人化ポイントの洗い出し
まずは現場での属人化ポイントを特定します。
- 熟練者と未熟練者の作業比較
- 「この人しかできない」とされる工程のリストアップ
- トラブル発生時に特定の人に依存する状況の把握
- 引継ぎが難しいとされている作業の特定
精密機械メーカーA社では、各工程の「属人化度」を5段階で評価し、属人化度の高い工程から優先的にマニュアル化を進めるアプローチを採用しました。これにより、リソースを効率的に配分することができました。
2-2. 熟練者の作業観察と分析
属人化されている作業を詳細に観察・分析します。
- 高速カメラによる動作分析
- 熟練者へのインタビュー(判断基準や感覚的な要素の言語化)
- 作業時の視線追跡
- 手の動きや力加減の測定
エレクトロニクスメーカーB社では、熟練検査員の目の動きを視線カメラで追跡・分析し、どのような順序で製品のどの部分を見ているかを可視化。この情報をもとに検査マニュアルを作成することで、熟練者並みの不良検出率を実現しました。
暗黙知を形式知に変換する手法
属人化の中核となる「暗黙知」を「形式知」に変換する手法を紹介します。
3-1. 定量化による見える化
感覚的な判断を数値化することで、誰でも再現可能にします。
- 「適量」→「5mL±0.5mL」
- 「しっかり締める」→「トルク12N・m」
- 「なめらかになるまで」→「粘度〇〇Pa・s以下になるまで」
- 「熱くなったら」→「表面温度60℃以上になったら」
自動車部品メーカーC社では、熟練者の「手応え」で判断していた締め付け作業を分析し、適切なトルク値を設定。電動トルクレンチの導入とあわせて誰でも同じ品質の締め付けができるようになりました。
3-2. 判断基準の明確化
良否判断や調整の判断基準を明確にします。
- 外観検査の合格基準(OK/NG見本の写真付き)
- 異常判断のためのチェックリスト
- 調整の目安となる基準値
- 五感を使った判断の言語化(「カラカラ」「ツルツル」などの擬音語・擬態語の定義)
視覚化・定量化による標準化のポイント
マニュアルの効果を高める視覚化・定量化のポイントを解説します。
4-1. 作業の視覚化テクニック
- 連続写真による動作の表現
- 動画とQRコードの活用
- 3D図面やアニメーションの活用
- 実物大の型紙や治具の活用
食品メーカーD社では、熟練者の「手際の良さ」を連続写真で分解し、各ステップの手の位置や姿勢を明示したマニュアルを作成。新人の習熟期間を従来の半分に短縮することに成功しました。
4-2. 定量的な基準の設定方法
- 測定器の活用(温度計、湿度計、トルクレンチなど)
- 比較サンプルの準備(標準サンプル、限界サンプル)
- チェックリストの作成
- 数値による管理基準の設定
電子部品メーカーE社では、熟練者の「見た目で判断」していた検査工程に対し、デジタルマイクロスコープと画像解析ソフトを導入。傷や汚れのサイズを数値化することで、検査基準を明確化しました。
製造品質を保証するチェックポイントの設計
品質保証の視点からチェックポイントを設計する方法を解説します。
5-1. クリティカルポイントの特定
製品品質に大きな影響を与える重要な工程や作業を特定します。
- FMEA(故障モード影響解析)の活用
- 過去の不良事例からの要因分析
- 熟練者が特に注意している点の抽出
- プロセス能力指数(Cp, Cpk)の分析
5-2. 効果的なチェックポイントの設計
- 自己チェックと他者チェックの使い分け
- チェックタイミングの最適化
- 視覚的なチェックシートの設計
- デジタルツールを活用した記録システム
事例に学ぶ:業種別の属人化解消成功例
実際の製造業における属人化解消の成功事例を紹介します。
6-1. 金属加工業F社の事例
熟練技能者の研磨技術を伝承するため、力加減センサーと動作分析を組み合わせたデジタル教材を開発。センサーからのフィードバックを基に、適切な力加減を体得できるシステムを構築しました。これにより、従来3年かかっていた技能習得期間を1年に短縮することに成功しました。
6-2. 化学メーカーG社の事例
調合工程における熟練者の「感覚」を分析するため、プロセスデータ(温度、圧力、粘度など)と製品品質の相関を統計的に分析。その結果を基に、各パラメータの最適範囲を特定し、自動制御システムを構築しました。これにより、熟練者でなくても高品質な製品を安定して生産できるようになりました。
6-3. 食品メーカーH社の事例
職人の「目利き」に頼っていた原料選別工程に画像解析技術を導入。AIによる良品判定システムを構築し、選別基準を標準化しました。さらに、AIの判定結果と熟練者の判断を継続的に比較・検証することで、システムの精度を向上させています。
まとめ:属人化を防ぐためのアクションプラン
製造現場の属人化を防ぐためのマニュアル作成のポイントをまとめます。
- 現状分析で属人化ポイントを特定する
- 熟練者の暗黙知を分析・言語化する
- 感覚的な判断を可能な限り定量化する
- 視覚情報を効果的に活用したマニュアルを作成する
- 品質に直結するクリティカルポイントを特定し、効果的なチェック体制を構築する
- デジタルツールを活用し、継続的な改善を行う
- 現場での実践と検証を通じてマニュアルを進化させる
属人化の解消は一朝一夕に実現するものではありません。しかし、本記事で紹介した方法を実践することで、「誰がやっても同じ品質」を実現する製造現場づくりに一歩近づけるはずです。マニュアルは単なる文書ではなく、組織の知恵を結集した「知的資産」です。継続的な改善を通じて、より強固な製造基盤の構築を目指しましょう。
この記事を書いた人
編集部