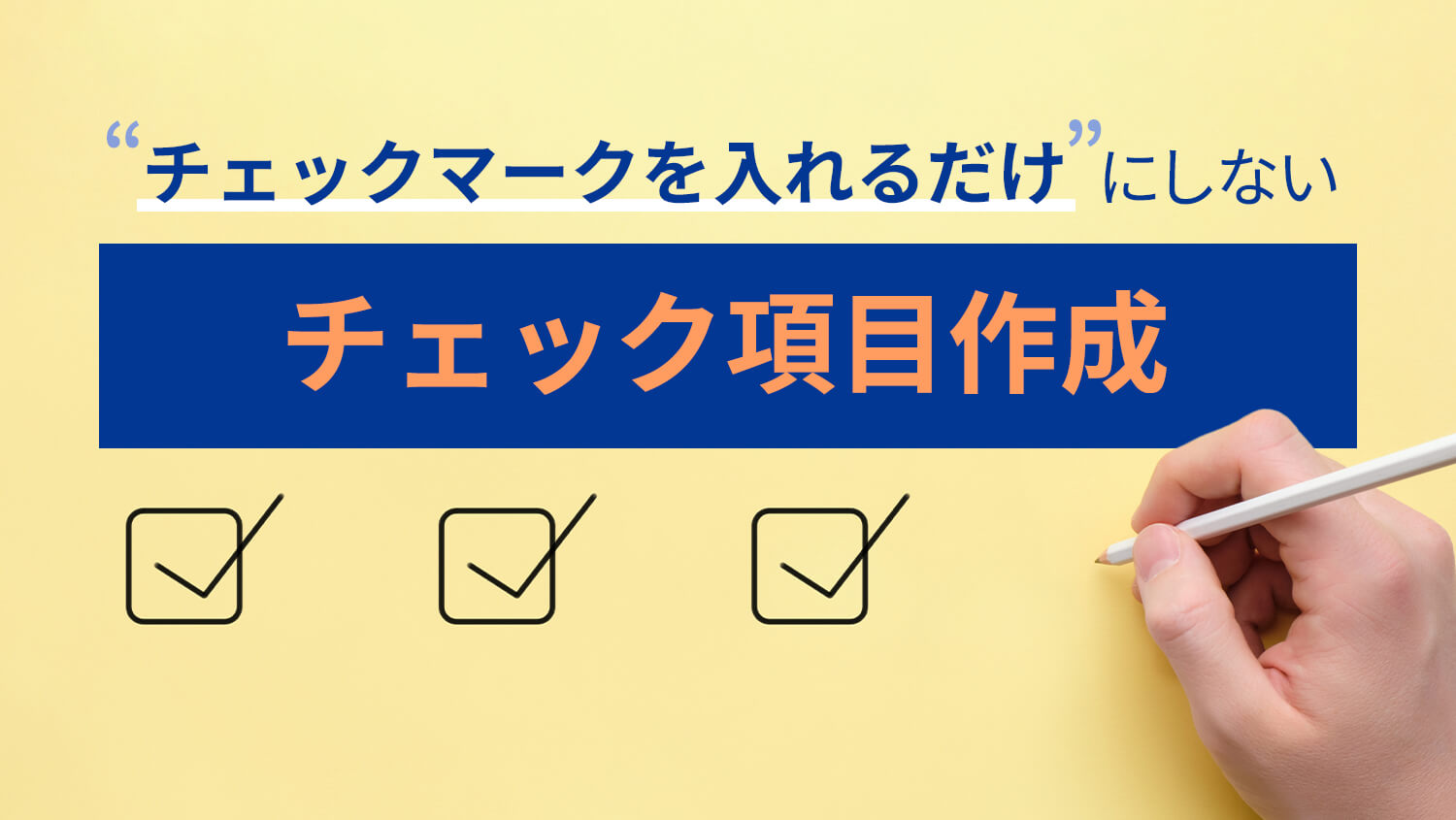
現場で役に立つマニュアルを作るうえで、もっとも重要なのは内容です。マニュアルの内容を充実させるための最大のポイントこそが「最小単位の作業」です。本記事では「最小単位の作業」を意識した製造マニュアルの作り方について、例を挙げながら解説します。
「最小単位の作業」とは?
本記事での「最小単位の作業」とは、工程の中に存在している「ひとつの判断をするまでの一連の作業」をいいます。
抽象的な定義だけではわかりにくいため、機械の始業点検を題材にして、実際に工程を最小単位の作業に分解してみましょう。
始業点検を題材にした工程の分解
とある印刷機械の始業点検に関するマニュアルを作成する際に、マニュアル作成者がまとめた作業は次のようなものでした。
- 機械の電源ボタンを押す
- 始業点検用の用紙をセットする
- セットした用紙に始業点検用のデータを印刷する
- 印刷した用紙を機械から取り出す
- 印刷した用紙に正しく印刷されたかを確認する
- 始業点検用のチェックシートに結果を記録する
- 印刷した用紙を記録として所定のファイルに保管する
早速、最小単位の作業に分解してみましょう。
各作業において注目すべき点は「作業者が合否判断をしているか」です。
たとえば、1の作業は電源ボタンを押すだけの単なる動作であり、合否判断はしていません(本当に押したかどうかというのは認知の問題です)。
上記の作業で判断が介在しているのは、5の段階です。
ここでは「正しく印刷されたかどうか」を判断しています。
6以降は明確な判断の記載はありませんが、実際には7が終わった段階で「始業点検が完了したかどうか」という判断をしています。
以上のことから、この印刷機械の始業点検を最小単位の作業に分けると、1~5の作業と6~7の作業の2つに分解できます。
マニュアル作成に携わった方であれば「最小単位の作業」という概念を意識していないとしても、上記のような工程の分解は当然やっていることだと感じるかもしれません。
ところが、例に挙げた始業点検について上記の工程の分解に従ってマニュアル化すると、役に立たないマニュアルができあがります。
なぜなら、最小単位の作業に分ける前のそもそもの作業が現場の実態を捉えられていないからです。
本当に最小単位の作業か?
先に挙げた始業点検の例ですが、一見するともっともらしい作業が羅列されています。
ところが、今回のマニュアル作成者がまとめた作業は実際の作業を網羅できていませんでした。
始業点検において判断が介在しているのは、上記5だけではなかったのです。
始業点検の実態を反映して作業を追記すると次のようになります。
- 機械の電源ボタンを押す
- 機械が正しく起動したかを確認する
- 始業点検用の用紙をセットする
- 用紙が正しくセットされたかを確認する
- セットした用紙に始業点検用のデータを印刷する
- 印刷した用紙が正しく出てきたかを確認する
- 印刷した用紙を機械から取り出す
- 印刷した用紙に正しく印刷されたかを確認する
- 始業点検用のチェックシートに結果を記録する
- 印刷した用紙を記録として所定のファイルに保管する
上記のとおり、当初は7段階だと思われていた始業点検の作業が10段階に増えました。
これに従って最小単位の作業に分けると、1~2、3~4、5~6、7~8、9~10の5つに分解できます。
さきほどは2つに分解した始業点検でしたが、本当は5つに分解できたのです。
今回の例でマニュアルに記載すべき作業が漏れていることに気付けた理由は、最小単位の作業を意識したためです。
最小単位の作業は工程内での「判断」を指標にして分解します。
当初の1~5の作業を最小単位の作業として見たときに、本当に1~5の間に「判断」が存在していないのかという疑問が生まれ、作業の見落としに気付いたのです。
最小単位の作業を意識し、分解の指標である「判断」に注目することで、マニュアルの問題を表面化させられます。
「判断」に着目して工程を見直す
ひとつの工程における作業を捉えるうえで見逃しやすいのが「判断」です。
ボタンを押す、何かを取り出すといった「動作」は、はっきりと目に見えるため作業を把握するときに見逃すということはまずありません。
しかし「判断」は基本的に目に見えないものであり、ベテランの作業者だと無意識で行っているものも工程の中にはたくさん潜んでいます。
マニュアルを作成する際は、工程の中に存在している「判断」は性質上見逃しやすいものだ、という意識を持って作業を見直すことが重要です。
とくに注意したいのは、製造業でよく利用するチェックシートの存在です。
今回例に挙げた始業点検も、チェックシートに注目しすぎたために工程内のほかの判断を見逃した場合の典型例です。
目に見える「判断」であるチェックシートを利用した作業を盛り込むと、何となく作業のすべてが記載されているように見えてしまいます。
しかし、実際には工程の中にさまざまな「判断」が隠れています。
最小単位の作業に正しく分けるために、工程内に潜む「判断」をすべて見つけ出しましょう。
意味のある作業に改める
最小単位の作業を意識することで、マニュアルを作成するために必要な本当の作業が見えてくることはご理解いただけたでしょう。
しかし、最小単位の作業を意識することによるメリットはこれだけではありません。
工程を最小単位の作業に分けることで、製造マニュアルに潜む「意味のない」記載にも気付けるのです。
改めて始業点検の例を題材にします。
さきほど10段階で表記した始業点検の作業を、そのまま始業点検のマニュアルに記載したとします。
その場合、作成したマニュアルにはまさに意味のない記載があるのです。
まずは、最小単位の作業として1~2を取り出してみます。
- 機械の電源ボタンを押す
- 機械が正しく起動したかを確認する
この記載の中で意味のない部分はどこでしょう。
それは、2の記載すべてです。
なぜなら「正しく起動した」と判断するための判断基準が記載されておらず、何をするべきかがまったくわからないからです。
マニュアルであるにもかかわらず、やるべき作業が読み取れないのは致命的な問題です。
2の作業を意味のある記載に替えると次のようになります。
- 機械の電源ボタンを押す
- 機械のランプが緑色に点灯するかを目視する
これで、正しく起動したかどうかの判断基準が「ランプが緑色に点灯すること」だと明確になりました。
最小単位の作業に分解することで、マニュアルの記載が本当に意味のあるものかがわかりやすくなります。
今回の始業点検の例で意味のない記載をすべて見直すと、最終的に次のようになります。
- 機械の電源ボタンを押す
- 機械のランプが緑色に点灯するかを目視する
- 始業点検用の用紙をセットする
- 用紙のセット位置が機械のマークと一致しているかを目視する
- セットした用紙に始業点検用のデータを印刷する
- 印刷した用紙が排出口でそろっているかを目視する
- 印刷した用紙を機械から取り出す
- 始業点検用のチェックシートの項目と印刷した用紙の状態を照合する
- 始業点検用のチェックシートに結果を記録する
- 印刷した用紙を記録として所定のファイルに保管する
※実際にマニュアル化する場合は、各動作をより詳細に記載するなどの作り込みが必要です。
最初に示した作業と比較すると内容が充実しており、最初の状態がいかに不十分な内容であったかがわかるでしょう。
最小単位の作業の考え方は、新しくマニュアルを作成するときだけでなく、マニュアルを見直すときにも活用できます。
最小単位の作業という観点から、マニュアルを読んでみてはいかがでしょうか。
なお、本記事で悪い例として挙げた「~を確認する」という表記は、使い勝手がよいためマニュアルを作る際に使ってしまいがちな言葉です。
このような表記は、実際のところ中身がない場合が往々にしてあります。
マニュアルを見直す際の要注意ワードのひとつとして「確認」という言葉は覚えておくとよいでしょう。
マニュアルもどきから脱却しよう
現場で必要とされないマニュアルがあれば、まずは内容が不足していて作業がわからないマニュアルもどきではないかを疑ってみましょう。
現場が必要とする情報が記載されていれば、多少の読みにくさ・わかりにくさがあっても現場で使われているものです。
貴重な時間と人員を割いてマニュアルもどきを作らないためにも、マニュアル作成に取り組む際は、ぜひ「最小単位の作業」を意識してみてください。
テクニカルライティングのソリューションにご興味がある方はこちらをご覧ください。
この記事を書いた人
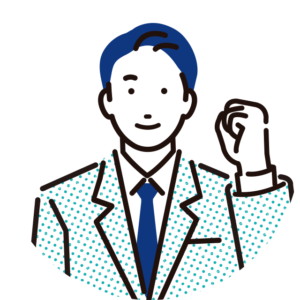
名池 令
製造業の品質管理部門に所属。製造現場の作業確認などを通して、日々品質の維持に勤しむ。製品の出来栄えが個人の力量に依存しないよう、誰でも安定して運用できる仕組み作りに取り組んでいる。標準とする作業や判断の指標を明確化するために、マニュアルやチェックシートの作成・見直しに力を入れている。VBAの作成を得意としており、部署の垣根を越えて各種業務の自動化も推進。